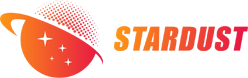
作为一种体心立方结构的难熔金属材料,由于钽与氧和氮原子的高反应性,会在表面形成介电强度高的Ta2O5氧化膜层,使得钽被大量用于电气和电子行业,特别是作为需要储存大量电势能的电容器[1,2]。此外,钽具有化学惰性和优异的耐腐蚀性,也可被应用于外科植入物和化工装备制造[3]。然而,钽的熔点(2996℃)高,是钛(1668℃)的1.8倍,导热性能好,导热系数(57.5W·m-1·K-1)是钛的3.8倍。因此,金属钽复杂构件的成形和加工难度较大。在过去50年中,金属钽零部件的制造大多是先采用粉末冶金法或电子束熔炼法获得钽金属的锭坯,再经塑性变形、焊接以及热处理后获得最终产品[4,5]。但这显然无法满足产业升级以及个性化医疗对多孔钽植入体等金属钽复杂构件的迫切需求。
近年来,数字化驱动的先进制造工艺迎来了高速发展时期,以激光选区熔化(selectivelasermelting,SLM)和电子束选区熔化(selectiveelectronbeammelting,SEBM)为代表的粉末床熔融增材制造装备和工艺不断成熟,其生产的钛合金零件在医疗、航空、航天等领域已经取得了规模化的应用,为金属钽的制造与生产提供了新工艺[6,7]。相比于传统加工技术,增材制造技术在金属钽的加工方面具有明显的优势[8-11],如:材料利用率高,以构件的三维模型为模板使得毛坯件尺寸接近最终产品,减少了加工余量,降低了生产成本;加工流程简化、缩短,提高了生产效率,且可实现个性化定制。因此,采用增材制造技术制备金属钽构件,实现金属钽复杂构件的高质量成形,对于满足产业升级以及个性化诊疗服务,具有重要的科学价值和应用价值。
本文主要介绍了增材制造用钽粉末原料的研究现状,综述了增材制造技术制备金属钽的微观组织与力学性能,随后结合作者团队的相关工作,讨论了增材制造医用多孔钽材料的研究及应用现状,分析了钽金属增材制造技术当前存在的一些问题,并为未来金属钽增材制造技术的发展提出了建议。
1 增材制造用钽粉原料的现状
金属粉末是增材制造技术的原料基础,流动性优良和堆积密度高的球形粉末是增材制造技术的首选原料[12,13]。然而,由于金属钽熔点高,传统的球形粉末制备工艺,如:气雾化等方法难以实现球形钽粉的制备。另一方面,传统电容器用钽粉的制备工艺,如氟钽酸钾钠还原法、氢化破碎等方法,所得的粉末粒度过小(<10μm)、形状复杂且基本没有流动性,无法满足增材制造技术的工艺需求[14]。
随着增材制造装备的成熟以及难熔材料复杂构件需求的增加,2015年开始各国科研机构及粉末制造企业先后投入了大量精力用于球形钽、钨以及钼等难熔金属粉末的工艺开发[15-17]。表1给出了各国相关企业商业化销售的球形钽粉的基本性能参数。可以看出,球形钽粉的制备主要是采用等离子球化(plasmaspheroidization,PS)和等离子旋转电极雾化(plasmarotatingelectrodeprocess,PREP)技术。
加拿大TENKA公司[20,21]作为全球等离子球化技术的商业化先行者(图1a),在2015年实现了增材制造的球形钽粉的商业化销售,美国环球卓越金属有限公司(GlobalAdvancedMetals)以及中国的北京科技大学、西北有色金属研究院、星尘科技等也先后采用等离子球化技术制备出了球形钽粉,如图1c所示(引自星尘科技官方网站)。但PS技术的设备投资大、运行成本高,且该技术是以粉末为原料制造粉末,由于成本等因素,限制了该类粉末的规模生产和应用。
PREP技术是目前工业生产高品质球形金属粉末的主要方法之一,如图1b和图1d所示。与PS技术相比,PREP技术是以金属棒材为原料,在生产成本、粉末形貌和杂质含量的控制优势明显,然而,PREP技术生产的粉末中45μm以下的粉末收得率一般不足10%,难以满足SLM技术的需求[19]。因此,通过装备升级和工艺优化,进一步提高PREP技术的细粉收得率是该技术在增材制造领域面临的主要挑战。
2 增材制造金属钽的研究现状
2008年,英国利物浦大学的Fox等人[23]首次采用SLM技术在CoCr合金表面制备钽金属涂层,此后,增材制造成形钽材料的研究开始成了领域内的一个热点。从技术角度来看,主要是以激光选区熔化、电子束选区熔化以及电弧送丝增材制造等技术为主。作为纯金属材料,钽在成形过程中的组织演变规律较为简单。因此,根据报道的金属钽结构形式,分别从实体钽和多孔钽的研究现状进行阐述。
2.1 增材制造技术制备金属钽的组织与性能
图2给出了增材制造工艺制备的金属钽的微观组织。可以看出,通过工艺参数的优化,现阶段增材制造技术制备的钽金属内部缺陷得到了有效控制,致密度均可达99.9%以上[18,22,24-27]。与大多数增材制造制备的金属材料相同,金属钽的微观组织同样表现为沿生长方向外延生长的粗大柱状晶结构。其中,SEBM技术成形材料柱状晶的特征最为明显,如图2c所示,柱状晶的宽度为165.22±3.44μm[22]。
Zhou等人[26]近期的研究结果表明,SLM技术成形的金属钽在经过三重高温退火后,其组织将由粗大的柱状晶转变为等轴晶,这对于消除增材制造金属材料各向异性至关重要,如图3所示。作者认为是由于高温退火消除了SLM成形件内部巨大的内应力,同时位错运动在高温下被充分激活,发生的位错滑移或攀移为柱状晶向等轴晶的转变提供了必要条件。
图4分析了增材制造金属钽材料的室温力学性能。按照相关材料标准,氧含量300µg/g是钽中氧含量的上限。因此,为了系统说明增材制造钽金属的力学性能,在图4a,4b中分别列出了屈服强度和延伸率与氧含量的关系。可以看出,由于研究初期粉末制备技术的原因,部分增材制造钽金属的氧含量超过了标准规定的上限。另一方面,SEBM技术所用粉末氧含量较低,材料的屈服强度与传统工艺基本吻合,而SLM制备的钽金属屈服强度的分散性较大。例如,氧含量1800µg/g的钽金属[28]屈服强度要低于低氧含量的情况[18,25],这是可能由于成形样品内残余的孔洞缺陷导致的致密度不足引起的。
从图4b的数据中可以看出,增材制造技术制备的金属钽延伸率随氧含量的变化规律与传统制备工艺基本吻合[29]。随着氧含量的增加,试样的延伸率从50%降低至约2%,这表明增材制造钽金属的延展性能对氧等杂质元素含量同样敏感。在力学性能中,材料的屈服强度和伸长率被认为是钽在高应变率应用中的主要性能[30]。根据German[31]的观点,粉末冶金法制备钽金属的屈服强度和伸长率应分别高于396MPa和30%。同时,参考德国PLANSEE公司制造的商品钽,电子束熔炼和粉末烧结钽的屈服强度和伸长率分别为390MPa和31%及420MPa和18%[32]。因此,增材制造技术制备的钽金属在力学性能方面还有很大的提升空间,如图4c所示,尤其是在强度和延伸率的合理匹配中。
2.2 增材制造技术制备多孔钽材料的性能
多孔钽是一种与人体骨具有相近孔结构的泡沫状多孔金属材料,与其他医用金属材料相比,多孔钽具有高容积孔隙率、低弹性模量及高表面摩擦系数的典型特性,从而被认为是一种比较理想的骨替代材料[33]。但由于钽金属熔点高,通过传统的加工工艺难以实现复杂多孔结构的加工制造,直到20世纪90年代初,Kaplan等人[34]通过化学气相沉积技术实现了多孔钽的制备,并由美国Zimmer公司实现了商业化销售。目前,Zimmer公司的标准化TrabecularMetal™系列多孔钽产品基本垄断了各国钽金属的植入体市场[35]。近年来,随着个性化诊疗理念的逐步普及以及国民健康意识水平的提高,临床对个性化骨科植入物的需求呈现出了爆发性的增长。因此,在钛合金多孔植物中取得成功后,采用增材制造技术制备与Zimmer公司多孔钽植入体结构与性能相比拟的多孔钽材料,就成为了增材制造和骨科临床领域的交叉研究热点。
表2列出了现有文献报道的多孔钽材料的结构与性能,并与Zimmer公司采用CVD技术制备的多孔钽材料进行了对比。可以看出,增材制造技术制备的多孔钽材料,其孔结构形式主要包括:1)随机型孔结构(stochasticstructure,SS),如图5a所示。通过工艺参数控制,采用高能束将粉末材料部分熔化,即利用粉末颗粒间的缝隙形成三维联通孔隙;2)规则有序型孔结构,也可称为点阵结构(latticestructure,LS),如图5b,5c所示,是以杆或板以按类似晶体点阵结构的方式构筑而成的多孔结构。随机型孔结构是通过工艺参数的改变来实现孔隙参数的调整,其孔隙率和孔径的可控范围较窄。相比之下,点阵型有序孔结构,在增材制造钛合金骨科植入物中已经获得验证,可以自主的设计孔结构和孔径尺寸,与个性化诊疗的概念完全契合[40]。因此,采用增材制造技术不但可以实现与Zimmer公司多孔钽材料(图5d)相同的孔结构,通过改变三维模型设计,还可以实现孔结构参数与力学性能的按需调控。
力学性能是医用金属材料的最为重要的技术指标之一。足够的强度可以为组织长入提供支撑,合适的弹性模量可以有效地降低应力屏蔽,从而有力促进植入体的初期稳定性。图6对表2中的力学性能进行了分析,在同等密度条件下,增材制造技术制备的多孔钽强度要低于CVD技术,但二者均达到了人体松质骨的强度,如图6a所示。强度差异是由于CVD制备的多孔钽中残留有1%(质量分数)的碳[39],导致其强度远高于纯钽。根据Gibson和Ashby等人[41]的研究,多孔金属材料相对密度和强度之间存在一定的对应关系,可以用于指导个性化多孔植入体的结构设计[38,42]。但目前公开报道多孔钽材料的力学性能数据较少,尤其是弹性模量数据。
需要引起注意的是,国际标准钽金属植入体标准ISO13782-1996以及中国医疗行业标准YYT0966-2014中,规定钽植入体的氧含量上限是300μg·g-1,然而,现有部分报道所用的粉末原料的氧含量超过了300μg·g-1。
3 增材制造金属钽的应用现状
装备与工艺的不断成熟,促使增材制造多孔钽材料在临床的应用步伐不断向前推进。由于临床对多孔钽植入体的迫切需求和巨大市场潜力,十三五期间,作者单位在科技部重点研发计划的支持下,突破了医疗级球形钽粉的制备、专用成形设备研发以及成形与后处理工艺等多项关键技术,并于2018年4月18日,在陆军军医大学第一附属医院完成了全球首例粉床电子束增材制造个性化多孔钽植入体的临床应用考核。在2016年~2020年期间,先后完成了5大类共计65例个性化多孔钽植入体的制备,临床应用效果良好,如图7所示。
4 总结与展望
金属钽具有优异的理化性能,在化工、电子、电气以及医疗行业中应用广泛。近年来,增材制造装备的普及与工艺的成熟,为钽金属复杂构件的制备提供了全新的加工方法,并已在个性化骨科植入体的制备中取得成功。但由于研究时间有限,钽金属的增材制造同样面临些许挑战,具体包括:
1)现有球形钽粉的价格大多为冶金级钽粉的2~3倍,极大限制了增材制造技术在钽金属加工领域的应用。因此,通过粉末制备工艺优化,降低粉末的生产成本以及粉末收得率,是增材制造技术在钽金属制品加工中面临的挑战之一。
2)经过近5年的研究,增材制造钽金属的研究取得了很大的进步,解决了无粉末原料的困境,中国也出台颁布了粉末原料的国家标准《增材制造用钽及钽合金粉》(GB/T38975-2020),现有报道的材料成分、室温力学性能基本达到传统加工工艺。但应注意到,增材制造钽金属的研究还处于初期,钽金属增材制造的材料及产品标准还未出台,关于致密钽金属的性能研究还不够深入,例如:材料的耐腐蚀性、高温力学性能以及疲劳性能等相关工作还未见报道。因此,加快推进钽金属材料的综合性能研究,全面对标传统制备工艺,尽快制定增材制造钽金属的材料及产品标准,是增材制造钽金属亟需开展的系统研究工作。
3)增材制造的个性化多孔钽植入体虽然已应用于临床,但骨科医疗植入物属于三类医疗器械,各个国家的食品药品监督管理局对医疗器械都有严格的准入审批制度。因此,要将增材制造的个性化多孔钽植入体正式批量化生产,需尽快完成基础实验研究,按照相关规定进行临床试验过程和审批流程,才能推进增材制造多孔钽临床应用的步伐,早日造福患者。
4)增材制造钽金属的应用目前主要集中在骨科植入物方面,还未见有其他领域的应用报道。因此,结合增材制造技术的工艺特点,进一步推广拓展该技术在原子能、航空航天等领域的应用,对推动该技术的普及与进一步发展具有重要的意义。
参考文献:(c)1994-2022 china Academic Journal Electronic publishing House. All rights reserved. http://www.cnki.net
星尘科技采用射频等离子体球化制粉设备,制备的球形钽粉由于其优异的性能,在多个领域有着广泛而具体的应用。以下是一些主要应用及其具体描述:
1. 医疗植入物
应用场景:3D打印髋关节假体(如髋臼杯)、骨修复植入物、牙科植入物等。
具体描述:钽具有优异的生物相容性和抗腐蚀性,能与人体组织良好融合,促进骨细胞的生长和愈合。因此,球形钽粉广泛用于制作植入物,通过增材制造工艺,可精准定制复杂几何形状的结构以满足个人化医疗需求。
2. 航空航天领域
应用场景:高温部件、火箭喷嘴、航天器燃烧室。
具体描述:钽具有高熔点、优良的抗热震性能和导热性能。使用球形钽粉通过增材制造(3D打印)技术,可以制造具有复杂结构、减轻重量的耐高温零部件,从而提升飞行器的燃烧效率和可靠性。
3. 化工与微通道反应器
应用场景:高腐蚀环境下的换热器、微通道反应器。
具体描述:球形钽粉可用于制造微通道反应器的核心部件,这些设备需承受高温、高压以及强酸强碱的腐蚀环境。钽的耐化学腐蚀性和卓越的机械性能,使其成为化工装备制造的理想选择。
4. 电子工业
应用场景:钽电容器、薄膜电阻。
具体描述:钽的高电容性和低泄漏特性,使得其在电子元件中应用广泛。球形钽粉因流动性好、纯度高,适用于等离子喷涂或粉末冶金工艺,制造出高性能的电子元器件。
5. 国防工业
应用场景:军用高性能装甲、弹头及穿甲弹。
具体描述:钽的高密度和优异的抗冲击性能,使其在防护和武器材料中有重要应用。通过使用球形钽粉,能够制备高致密度的零件,提升武器装备的破坏力和耐久性。
6. 实验室及科学研究
应用场景:高端设备配件及靶材。
具体描述:用于电子束熔炼、真空系统中的高温耐腐蚀部件以及各种先进薄膜材料的溅射靶材。球形钽粉的高纯度及均匀粒径分布可确保实验结果的精确性和材料的稳定性。
这些应用充分体现了球形钽粉在高端制造和新兴技术领域的重要性。通过结合增材制造技术,其潜在用途将不断被挖掘和拓展。
如有需要,欢迎联系我们的专业人员:郑经理13318326187