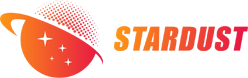
多孔钽是一种与人体骨具有相近孔结构的泡沫状多孔金属材料。与其他医用金属材料相比,多孔钽具有高容积孔隙率、低弹性模量及高表面摩擦系数等特性,是一种比较理想的骨替代材料[1],其应用前景有望赶超目前临床应用最广泛的钛合金,成为骨科临床应用材料研究的新方向[2]。Zimmer公司[3]采用气相沉积技术制备的多孔钽植入体已经在临床得到规模应用,对52例患者长达15年的跟踪结果表明,无一例病患出现炎症、植入体松动、骨吸收和髋臼移位等问题,也无一例病患需要重新实施髋臼翻修,充分证明了多孔钽植入体在临床应用初期和远期的稳定性。
随着精准医疗理念的普及,临床对植入物提出了个性化的需求,如何解决标准化植入体缺乏个体匹配性的问题,成为医学界和工程界共同关心的话题和研究热点[4]。增材制造技术的出现使得个性化植入体的工业化制备变为现实,并且已经在钛合金植入体的制造中取得了成功[5]。现有研究结果表明,流动性优良和堆积密度高的球形粉末是增材制造技术的首选原料[6]。然而,由于金属钽熔点高(2996℃),传统的球形粉末制备工艺(如气雾化法)难以实现球形钽粉的制备;另一方面,传统电容器用钽粉的制备工艺,如氟钽酸钾钠还原法、氢化破碎等,所获得的粉末粒度过小(<10μm)、形状复杂且基本没有流动性,无法满足增材制造的技术工艺需求[7]。
射频等离子体由于具有温度高(约104℃)、等离子体炬体积大、能量密度高、基本无污染、传热和冷却速度快等优点,是制备组分均匀、球形度高、流动性好的球形粉末的优秀方法[8]。尤其在高熔点、难熔金属球化处理方面,射频等离子体产生的高温可提供足够的能量使难熔金属粉末在穿越等离子体时迅速吸热、熔融,并在表面张力作用下缩聚成球形,在极短的时间内骤冷凝结形成球形粉末,是获得致密度高、球形度好、纯净度高的球形粉末的有效手段,较其他工艺具有较大的技术优势。国内外学者目前已利用射频等离子体技术成功制备了球形W、Mo等难熔金属以及氧化铝陶瓷粉末[8‒10],而利用射频等离子体制备球形钽粉还未见相关报道。本文以冶金级钽粉为原料,通过射频等离子体球化技术制备增材制造用球形钽粉,研究了球化处理工艺对粉末特性的影响及加料速率对球化率的影响,以期为球形钽粉的制备和应用提供依据。
1实验材料及方法
1.1原料及球化装置
实验原料采用中国宁夏东方钽工业有限公司提供的冶金级钽粉,粉末平均粒径为12μm。
使用TekSphero40型射频等离子体系统(TeknaCo.Ltd.Canada)对原料钽粉进行球化处理,球化装置如图1所示。该系统主要包括射频等离子炬、可编程逻辑控制器(PLC)、射频发生器、粉末供给系统、真空系统、粉末收集室以及水冷系统。实验以高纯氩作为等离子气体,在电场激发下产生等离子体,以高纯氩气作为鞘气,用于冷却等离子体系统的石英管。粉末原料通过氦气(载气)以恒定的供给速率送入等离子炬,在此过程中,粉末颗粒被迅速熔化并经历固‒液相变,液态颗粒在表面张力的驱动下球化、凝固,最终被收集在粉末回收罐中,实验所用的工艺参数如表1所示。
图1等离子球化装置结构原理图
Fig.1Schematicillustrationoftheradiofrequency(RF)plasmaspheroidizationprocess
表1射频等离子球化钽粉的工艺参数
Table1ProcessingparametersforRFplasmaprocessing
1.2性能检测
采用扫描电子显微镜(JEOL,JSM-6460,scanningelectronmicroscope,SEM)观察球化前后钽粉的形态变化,并在相同放大倍数下,选择至少10个视场进行不同供给速率下粉末球形率的统计。使用Malvern激光衍射分析仪(MalvernMS2000,Worcestershire,UK)分析粉末的粒度分布。通过X射线衍射(BrukerD8AdvancePhaser,X-raydiffraction,XRD)表征粉末的相组成。根据ASTMB213-13和ASTMB212-13,利用霍尔流量计对钽粉的流动性和松装密度进行测量,每组数据至少测定三个点,取平均值。采用原子发射等离子体光谱对球化前后钽粉的C、H、O元素的变化进行测定。
2结果及讨论
2.1球化工艺对粉末球化效率的影响
射频等离子体已成功用于W、Nb、Al2O3等高熔点难熔粉末的球化,研究结果表明,粉末供给速率是决定球化效率的关键因素[8-11]。因此,本文重点研究了粉末供给速率对钽粉球化效率的影响,其他工艺参数均参照表1所示的设备供应商提供的建议值。
不同供给速率球化后的钽粉形貌如图2所示。可以看出,当粉末供给速率为10g·min-1时,球化后的钽粉表现出良好的分散性,此时球化率为91%。图3所示为粉末供给速率对钽粉球化率的影响,随着供给速率的提高,粉末球化率从91%降低至20%以下,当供给速率增加到40g·min-1以上时,仅有一小部分颗粒球化。
图2不同供给速率球化后钽粉的微观形貌:(a)原始钽粉;(b)10g·min-1;(c)20g·min-1;(d)30g·min-1;(e)40g·min-1;(f)50g·min-1
Fig.2SEMimagesofthespheroidizedtantalumpowdersatdifferentfeedingrates:(a)rawpowders;(b)10g·min-1;(c)20g·min-1;
(d)30g·min-1;(e)40g·min-1;(f)50g·min-1
图3粉末供给速率对钽粉球化率的影响
Fig.3Influenceoffeedingrateonthespheroidizationefficiencyoftantalumpowders
钽粉颗粒完全球化所需要的能量可以按照式(1)来计算[12],
式中:Q为熔化全部钽粉所需的能量,v为球化时的粉末供给速度,d为粉末颗粒直径,ρ为密度,Cp为比热容,Tm为熔点,T0为环境温度,Hm为钽的熔化潜热。可以看出,粉末给料速度的提高将导致单位时间内需要的热量增加,而且粗颗粒要比细颗粒所需的能量高。因此,在本文所采用的工艺参数下,当供给速度为10g·min-1时,粉末获得的能量足够熔化被送入等离子体区域的钽粉,此时粉末颗粒的球化率最高。随着粉末供给速率的提高,单一粉末颗粒在一定条件下所能获得的热能逐渐减少,从而导致粉末球化率的快速下降。另一方面,供给速率过大也可能使部分颗粒的运动轨迹偏离等离子体的高温区,从而导致能量利用不足[13],也会降低钽粉的球化率。
在图2中还发现,在较高的供给速率下,大尺寸颗粒比小尺寸颗粒(<5μm)更易被球化。Yu等[14]在射频等离子体球化钨粉的过程中也观察到了类似的现象。这可能是由于小尺寸粉末颗粒在等离子球化过程中出现的“反混”效应,将小颗粒从高温区域逸出[15],从而导致小尺寸粉末的球化效果较差。
2.2球化参数对钽粉物理性能的影响
为了确保工艺过程的稳定性和成形件质量,增材制造技术所需粉末原料通常具有较高的松装密度(超过理论密度的50%)和良好的流动性。对于商用冶金级钽粉,松装密度仅为理论密度的35%,并且原料粉末由于粒度细小,粉末之间的范德华力较强,粉末团聚现象严重,同时不规则状的粉末间架桥现象严重,导致流动性几乎为零。图4给出了粉末供给速率对等离子体球化钽粉物理性能(流动性和松装密度)的影响。由图可知,经等离子体球化后,钽粉的流动性得到显著改善;当粉末供给速率为10g·min-1时,获得的钽粉松装密度达到理论密度的56%,流动性达到了13.83[s·(50g)-1]。这是由于球化后球形粉末颗粒堆积时接触面小,颗粒间的空隙减小,架桥现象明显减少,使松装密度和振实密度得到显著改善,达到了增材制造技术的要求。
图4粉末供给速率对钽粉流动性和松装密度的影响
Fig.4Influenceoffeedingrateontheflowabilityandapparentdensityoftantalumpowders
2.3球化处理对粉末粒度及粒度分布的影响
图5给出了球化前后钽粉的粒度分布测试结果。可以看出,冶金级钽粉原料的粒度分布较宽,平均粒径为12μm。当粉末供给速率为10g·min-1时,球化后钽粉的粒度分布稍有变化,平均粒径增大至15μm。这是由于在等离子球化过程中,尺寸较小的颗粒熔融后会发生相互碰撞、粘结,然后长成更大尺寸的颗粒。另外,小尺寸颗粒有可能会发生局部过熔,导致其气化,凝结在球化室内壁上。因此,最终收集到的球形粉末中的小尺寸粉末的量减少,球化后的钽粉粒度分布更为集中。另外,从以上分析可以看出,等离子球化制备的球形粉末粒度及其分布主要是由原始粉末粒度决定,因此,为了得到粒度分布窄的球形粉末,应严格控制原始粉末的粒度分布。
图5球化前后钽粉粒度分布
Fig.5Particlesizedistributionsoftantalumpowderbeforeandafterspheroidization
2.4球化处理对粉末成分和物相组成的影响
球化前后钽粉中杂质元素的含量(质量分数)如表2所示。由于整个球化过程中的气氛保护,球化前后钽粉中的间隙元素含量没有发生显著变化。另外,图6的球化前后钽粉X射线衍射图表明,球化后钽粉没有出现其它相,充分验证了射频等离子体球化技术制备球形钽粉的可行性。图7给出了球化后钽粉的表面形貌及截面照片。如图所示,球化后的钽粉表面光洁,球形度良好;对粉末进行截面检查未发现有空心粉缺陷,充分确保了增材制造时的工艺稳定和成形零件的质量可靠。
表2球化前后钽粉杂质元素质量分数
Table2Chemicalcompositionsofimpurityelementsintantalumpowdersbeforeandafterspheroidization
图6球化前后钽粉X射线衍射图
Fig.6X-raydiffractionpatternsoftantalumpowdersbeforeandafterspheroidization
3结论
(1)以不规则状的商用冶金级钽粉为原料,采用射频等离子体球化技术成功实现了增材制造用球形钽粉的制备。
(2)粉末供给速率是决定粉末球化效果的关键工艺参数。当粉末供给速度为10g·min-1时,钽粉的球化率可达90%以上,此时钽粉的流动性为13.83[s·(50g)-1],松装密度为58%,达到了增材制造技术的要求。
(3)经过球化后,钽粉中的间隙元素含量没有明显增加,粉末表面光洁,内部未发现有空心粉等缺陷。
图7球化后粉末的表面(a)及截面(b)显微形貌图
Fig.7Surface(a)andcross(b)sectionSEMimagesoftantalumpowdersafterspheroidization
文章来源:https://pmt.ustb.edu.cn/cn/article/doi/10.19591/j.cnki.cn11-1974/tf.2020.02.009
星尘科技(广东)有限公司是一家专业从事3D打印、粉末冶金、表面工程等领域高端球形粉末材料研发、生产和销售的高新技术企业。公司坚持以射频等离子体球化金属粉末技术为指导,提供国际先进的产品和应用解决方案。
公司主要产品有球形钽粉及钽合金粉、球形钨及钨合金粉、球形钼及钼粉、球形铌及铌合金粉、球形钛及球形钛合金粉、球形难熔高熵合金粉、高端稀有难熔金属及复合球形粉,并提供射频等离子体球化服务、等离子体旋转电极雾化服务。3D打印服务、热等静压、注塑、粉末冶金等技术服务。
难熔金属粉末等咨询,欢迎联系我们郑经理13318326187。我们将热情为您解答。