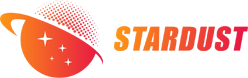
钨是一种重要的难熔金属,具有熔点高、密度 高、强度高、导热性好、热膨胀系数低等特点,广泛应用于航空航天,军事武器,电子和核工业等领域[1,2]。在国际热核聚变堆中,钨因其良好的耐热性、高溅射阈值及中子辐照下低活性等突出优点,被确定为面向等离子体材料的最佳选择[3]。然而,由于钨具有较高的熔点(3410 ℃)和室温脆性特征[4],使其难以通过传统的铸造或机加工方法进行制备和加工。通常,钨金属零件采用粉末冶金法制备,但烧结态的钨材料存在性能较差,相对密度较低,杂质含量不易控制等缺点,难以满足现代高尖端科学技术发展的需求。
近年来,随着纯钨材料应用领域的不断扩展,对零件的设计要求也越来越高。在穿甲弹,火箭喷嘴和核聚变装置中,所需钨零件通常拥有内孔,曲面以及沟槽等复杂结构,这就要求钨金属零件向三维形状设计更高的制造自由度发展。而传统成形方法在制造结构复杂的零件方面存在局限性[5]。
由于增材制造技术能够制备复杂的几何形状构件,对于钨材料加工来说是个不错的选择,该技术在开辟钨的新应用方面得到了广泛关注[6,7],但钨的固有脆性及增材制造过程中产生的微裂纹会损害其结构的完整性,阻碍了钨金属增材制造的发展和应用。目前研究主要集中于通过于粉末床的选区激光熔化技术(SLM)和选区电子束熔融技术(SEBM)探索纯钨及钨合金的制造[8,9],一方面利用 SLM 技术,表征钨增材制造时微裂纹形成方式和原理研究,同时开发适合钨合金材料的打印特定工艺参数[10,11];另一方面,通过 SEBM 增材制造技术的能源优势,即电子束,以及可以在熔化前预热金属粉末和承载板,从而减少变形和内应力,可制造出室温下易脆的钨材料[12,13]。
本研究采用 SLM 和 SEBM 技术制备纯钨,对比研究了打印工艺参数对纯钨的宏/微观组织和力学性能的影响。重点利用 SEM 和 EBSD 等表征技术,分析了裂纹的萌生位置及形成机制。通过对 2 种制备工艺的组织特征进行比较,为获得致密度高及裂纹少的钨材料具有重要的指导意义。同时,纯钨增材制造工艺参数、裂纹形成机制的研究也对其它具有高熔点材料的制备,如铌、钼等具有广泛的加工和应用意义。
1 实 验
SLM 和 SEBM 成形的钨粉均采用球形粉末,但因 2种设备熔融能力和成形工艺特点的差异,其粒度分布有所不同。SLM 成形采用的粉末采购自四川自贡硬质合金公司生成的还原钨粉,经等离子球化处理,成为球形钨粉,粉体形貌如图 1a 所示,粉末粒径 D10、D50 和 D90分别为 5.3、11.5 和 25.0 μm。SEBM 打印设备需要使用更粗的粉末以防止成形过程中发生“飞粉”现象,粉体的形貌如图 1b 所示,其 D10、D50 和 D90 分别为52.4、81.1 和 123.0 μm。2 种钨粉的化学成分见表 1,纯度均大于 99.9%。
SLM 成形纯钨试验使用的设备型号为Farsoon271M,该设备激光波长为 106 μm,光斑尺寸为130 μm。试验用基材采用 316L 不锈钢板,打印前基板预热至 100 ℃。打印过程中充入氮气(纯度 99.9%)作为保护气氛,当环境氧含量低于 200 μL/L 时,开始激光成形纯钨试验,主要试验参数:扫描间距和层厚分别为70 和 30 μm,激光功率和扫描速度如表 2 所示。为了更好地评估工艺参数的影响,使用体能量密度 E 作为输入样品中能量多少的度量,E 的数值如下公式:
式中,P 为激光功率,v 为扫描速度,h 为扫描间距,t为扫描铺粉层厚度。
SEBM 成形纯钨用设备型号为 Sailong S2,电子束电压恒定为 60 kV,采用 316L 不锈钢板作为基板。打印前基板预热温度为 850 ℃。打印过程中抽真空至 1×10-4Pa,然后充入氦气(纯度 99.9%)至 0.01 Pa。表3 为电子束熔化纯钨的具体工艺参数和 E 的计算值。扫描铺粉层厚 50 μm,扫描间距 100 μm,体能量密度 E 的数值如下公式:
式中,U 电子束电压,I 为电子束电流,v 为扫描速度,h 为扫描间距,t 为铺粉层厚度。
采用阿基米德排水法测量打印态样品的密度,并计算出纯钨样品的致密度。样品在进行机械磨抛后,用腐蚀液(10 mL 双氧水,10 mL 氨水配 80 mL 蒸馏水)腐蚀 90 s,最后将腐蚀后的样品进行显微组织分析。本研究 利用 光 学 显 微 镜( MeF3A)和 扫 描 电 子 显微 镜(JSM-6360LV)对纯钨样品的表面形貌和显微组织进行观察。利用电子背散射衍射(EBSD)技术分析晶粒大小及取向等,设备为型号 Helios Nanolab G3 UC 的双束显微系统。利用 X 射线衍射仪(Brucker D8 Discover 2500)进行纯钨样品的物相分析。利用维氏硬度仪(Buehler 5104,USA)测量样品的显微硬度,载荷 200 g,持续时间 10 s。
2 结果与讨论
2.1 纯钨块体及宏观表面形貌
图 2 所示为本研究中 SLM 与 SEBM 技术成形的纯钨块体。从外表面来看,纯钨的整体成形性较好,试样的表面均没有明显的孔洞、裂纹等缺陷。
图 3 为不同激光工艺参数条件下纯钨 SLM 成形试样正表面(垂直于建造方向)的宏观表面形貌。可以看出,随着能量密度的增加,打印态样品的表面裂纹数量增加,孔隙缺陷减少。裂纹主要表现为横向裂纹和呈 90°方向的纵向裂纹,其中横向裂纹即打印的道与道的结合处。增材制造的纯钨材料往往有严重的热裂纹倾向,一方面是由于钨的韧脆转变温度较高,室温下呈脆性的特征;另一方面是因为 SLM 过程中的快速冷却速率和所造成的巨大的温度梯度。在激光打印过程中,层与层之间存在较大的温度差,冷速较快产生大的热残余应力,当脆性材料的残余应力逼近甚至超过材料本身的屈服强度时,会促使裂纹萌生并扩展[14,15]。试验结果表明,可以通过优化工艺参数和提高基板预热温度来降低打印样品中的温度梯度,从而减小热残余应力[16]。通常,随着激光能量密度的升高,熔池温度升高,温度梯度和热残余应力增加,产生裂纹倾向增大。
图 4 为不同能量密度下 SEBM 成形试样的表面宏观形貌。随着能量密度的增加,打印态样品的表面由存在大量空隙、连续条状或未熔化粉末颗粒的粗糙表面(图4a)变为较平整、光滑的表面(图 4d)。从图 4f 还可以看出当能量密度达到 280 J/mm3时,未熔合缺陷减少,球化现象减弱甚至几乎没有,成形试样表面显示出连续的扫描轨迹,组织均匀,说明由工艺参数调控对纯钨成形样品表面有较大的影响,适当提高能量密度将有利于纯钨 SEBM 成形。SEBM 打印过程是粉末熔体的扩散和凝固相互竞争的过程。熔融金属的扩散受其表面张力和动态粘度的影响,金属钨熔体具较高的表面张力和粘度,从而具有较差的润湿性和较慢的扩散速度[17,18]。熔融的钨液滴在毛细管力驱动下低速地润湿固态表面,而大的温度梯度又驱使其快速凝固,因此熔滴在完全扩散之前发生凝固,并保持球状形貌,而不是扩散后形成平坦的一层。当输入样品的能量增大时,熔池温度升高,溶液动态粘度降低,凝固所需时间也越长,这样液滴能够得到很好的扩散,铺展效果更好,形成光滑、平整的表面。
综上可以看出,相比 SLM 成形,SEBM 成形的纯钨样品具有更高的表面质量和更少的裂纹缺陷。增材制造过程中,样品内部的冷速快、温度梯度高,会存在较大的残余应力,从而导致样品内部裂纹的产生。电子束打印过程能更好地降低热裂纹倾向[13],一方面,从打印方式上来看,是由于 SEBM 打印完一层后铺粉时,电子束都会对铺好的粉末进行预热,对凝固层再加热;另一方面,成型室的高真空度可以允许非常高的基板预热温度,打印过程中基板温度一直维持在 850 ℃左右,能够很好地降低残余应力,减少裂纹的产生。
2.2 致密度和力学性能
图 5 为 SLM 与 SEBM 成形纯钨的致密度和显微硬度随能量密度的变化。分析可知,SLM 和 SEBM 打印态纯钨的致密度和硬度与输入样品的能量密度呈正比关系,SEBM 打印的纯钨在较低的能量密度下可以达到较高的致密度。当电子束能量密度为 280 J/mm3,制备的纯钨样品达到 94.3%的致密度。而激光能量为 404.76 J/mm3,样品的致密度为 94.75%。致密度的高低很大程度上反映了样品内部孔隙等缺陷的多少。其中孔隙的形成是因为激光熔化过程中,成型室中的保护气体进入到熔池中来不及溢出,留在样品内形成了封闭孔隙。通常,较高的能量密度输入会增加溶液凝固时间,使气泡在凝固之前从熔池中逸出。激光能量不足导致气泡在凝固前从熔池中逸出的时间有限,并且,激光能量输入的减少将导致熔体缺乏熔合,产生未熔合缺陷[19]。SLM 制备纯钨样品时,虽然高能量会导致正表面宏观裂纹增多(图 3),但可能样品内部封闭的孔隙等微观缺陷更少,因此整体致密度更高,硬度(HV)也更高,达到了4174.8 MPa。孔隙和缺陷更少的 SEBM 打印态纯钨样品硬度最高为4370.8 MPa。
2.3 微观组织结构及 XRD 物相分析
图 6 为 SLM 和 SEBM 成形纯钨样品正表面的微观组织及 XRD 图谱。同图 3 类似,从图 6a 中 SLM 打印态纯钨组织可看出,裂纹位于熔道与熔道的搭接处,微观上表现为晶界位置。晶界在协调变形过程中,由于自身抵抗塑性变形的能力较弱,更容易成为裂纹源。与 SLM相比,SEBM 制备的纯钨晶粒较大(图 6b),这是由于打印过程中基板温度保持较高,冷却速度较慢,提供给晶粒长大的能量和时间更充足。此时,SEBM 打印样品内部的热应力累积也较小,产生裂纹的倾向更小。由图6c 可知,SLM 和 SEBM 打印态样品中的物相均为纯钨,无钨的氧化物峰的存在。
2.4 EBSD 数据分析及裂纹形成机制
通过扫描电镜的 EBSD 技术进行表征,进一步分析研究了 SLM 和 SEM 打印态纯钨样品的晶粒形貌及裂纹形成的机制。如图 7 所示,图 7a~图 7d 分别为 SLM 打印态样品的 EBSD 分析结果。从图 7a 扫描组织照片和图7b 反极图成像图可以看出,样品内部的裂纹由熔池搭接的长直裂纹和沿晶界扩展的裂纹构成。从图 7c 晶界取向形貌图可知,裂纹发生的晶界位置为大角晶界(>15°,蓝色区域),而小角晶界几乎不存在裂纹(<15°,绿色区域),计算可得出,小角晶界占全晶界比率为 81.8%,大角晶界占比 18.2%,晶粒平均尺寸为 56 μm。图 7d 为平均取向差形貌图,蓝色区域代表取向差较小的位置,这说明在该位置存在微裂纹,而绿色位置的有较大的平均取向差较大,为应力集中区域。同时在裂纹附近区域强度较高,这说明裂纹附近的应力较大,导致裂纹产生。
图 7e、7f 分别为 SEBM 打印态纯钨的 EBSD 结 果。计算可得出:SEBM 纯钨样品的平均晶粒尺寸为175.3 μm,小角晶界占比 98.7%,大角度晶界占比 1.3%。与 SLM 相比,SEBM 制备的纯钨的晶粒整体更粗大,小角晶界占比更多。小角度晶界能有效阻碍裂纹的进一步传播,而大角度晶界附近的应力较,易成为裂纹的来源,从而导致晶间裂纹。
综合以上结果分析及现有研究学者的报道[14,15],构建出图 8 所示裂纹形成机制示意图,对增材制造制备纯钨样品内部裂纹萌生位置及产生的机制进行阐述。宏观上来说,纯钨样品的裂纹多萌生于搭接区域,块体试样的成形需要产生道或层的搭接,而搭接所产生的影响就是熔池存在 2 个方向的散热趋势:一是纵向通过基板散热;二是通过相邻已凝固的沉积层进行横向散热,造成横向的温度梯度。此时裂纹是凝固收缩过程中形成的,产生于凝固最后阶段的固液混合区,此时混合区的临近固相区的位置存在凝固缩孔,孔隙极容易产生局部的应力集中,因此更容易促进裂纹的产生[20]。随着凝固的进行,样品内部温度降低,纯钨在低温(200~400 ℃)下呈脆性状态,凝固过程中产生的热应力也会导致低温开裂。从微观的角度分析,裂纹具有沿晶界扩展的特征,这是由于液相填充的晶界速度赶不上凝固速度或者裂纹形成速度,随着凝固的进行,残余液相的液膜在热应力的作用下被撕裂,从而形成裂纹。
3 结 论
1) SLM 和 SEBM 成形纯钨的致密度和硬度与输入样品的能量密度呈正比例关系。SLM 成形纯钨的致密度最高达到 94.3%,硬度(HV)达到 4174.8 MPa。SEBM成形纯钨的致密度最高达到 94.75%,硬度(HV)达到4370.8 MPa。
2) 与 SLM 相比,SEBM 成形的纯钨微裂纹较少。
SLM 样品内部裂纹多存在于搭接区域,SLM 和 SEBM制备过程中产生的裂纹均具有沿晶界分布的特征。
3) 从裂纹的产生机制来看,裂纹多萌生于大角度晶界。与 SLM 相比,SEBM 打印态样品的大角度晶界占比更少,小角度晶界数量更多,因此形成裂纹的倾向更 小。SEBM 成形过程中基体始终保温在 850 ℃,因此晶粒容易长大,温度梯度也较小,热应力更小,不容易开裂。
论文引用信息
第 51 卷 第 9 期 2022 年 9 月
稀有金属材料与工程
RARE METAL MATERIALS AND ENGINEERING
Vol.51, No.9
September 2022
星尘科技不仅供应高纯度稀有难熔金属球形粉末,包括球形钨粉、钼粉、铌粉、钽粉、钒粉、铼粉等。粉末品质稳定,粒度均匀,流动性优异!还提供金属 3D 打印快速成型一体化解决方案,从设计建模到成品交付,一站式服务!无论是航空航天、电子信息,还是医疗器械,精准满足您各种高端制造需求!
欢迎联系专业人员张经理了解更多详情!13318326185