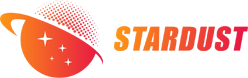
铌是最轻的难熔金属(密度为8.57g/cm3),铌及铌合金具有高熔点、较高的高温强度和比强度、良好的室温加工性能、焊接性和耐蚀性、无放射性的特点,是航空、航天发动机优选的热防护材料和结构材料[1-3]。传统的制备工艺存在零件形状相对简单和材料利用率低的问题[4]。基于粉末冶金技术的金属注射成形技术可以很好地解决这些问题,为低成本生产复杂形状的航空用零件提供了1种新的方法[5-7]。而粉末注射成形要求原料流动性好,形状呈近球形,普通铌粉难以满足该要求[8-9]。
射频等离子体由于具有温度高(约104℃)、等离子体炬体积大、能量密度高、无电极污染、传热和冷却速度快等优点,是制备组分均匀、球形度高、流动性好的球形粉末的良好途径[10-11]。尤其在难熔金属球化处理方面,射频等离子体产生的高温可提供足够的能量使难熔金属粉末在穿越等离子体时迅速吸热、熔融,并在表面张力作用下缩聚成球形,在极短的时间内骤冷凝结形成球形粉末,是获得致密度高、球形度好、纯净度高的球形粉末的有效手段,较其他工艺具有较大的技术优势。国内外学者目前已利用射频等离子体技术成功制备了球形W、Mo、Ta等难熔金属粉末[12-14],而利用射频等离子体制备球形铌粉还未见相关报道。
本文以不同粒度、不规则形状的微细Nb粉为原料,通过射频等离子体球化制备微细球形Nb粉。研究球化处理对粉末特性的影响及加料速率对球化率的影响,以期为球形Nb粉的制备和应用提供实验依据。
1实验
实验原料采用北京兴荣源公司提供的费氏粒度为24.83,31.02和59.74μm的FNb-2型铌粉,产品纯度大于99.9%,粉末形状为不规则形。采用自行研制开发的100kW型射频等离子体微粉处理装置对Nb粉进行球化处理,实验装置如图1所示。主要包括射频感应等离子发生系统(频率3.5MHz,功率100kW)、三层水冷石英等离子体灯炬、不锈钢冷却室、振动螺旋粉末喂料系统、供电及供气系统、产品收集系统等。
实验过程为:首先,以氩气为中心气和边气建立稳定运行的等离子体炬,输出功率75kW,系统负压85kPa,采用氩气为载气将Nb粉经喂料系统、由送粉枪轴向送入等离子体炬中。粉末在穿过等离子体高温区时迅速吸热、熔融,并在表面张力作用下缩聚成球形,在极短时间内骤冷凝结,形成球形粉末,经粉末收集系统收集,详细工艺参数如表1所列。
采用LEO-1450型扫描电镜对粉末进行形貌和微观结构观察;采用D/MAXRB型X射线衍射仪进行物相组成分析;采用LMS-30型激光粒度分析仪对粒度分布进行表征;松装密度、振实密度和粉体的流动性按照国标GB/1479-1984,使用霍尔流量计测定。
2 结果与分析
2.1 不同粒径铌粉的等离子体球化
图2所示为送粉速率为2g/min时,粒度分别为24.83、31.02及59.74μm的不规则铌粉球化处理前后的SEM照片。由图2可以看出,原料铌粉经等离子体球化处理后得到球形度高、分散性良好的铌粉(如图(b),(d),(f))。粉末团聚现象消失,球化率可达100%。
图3为球形铌粉(24.83μm)表面和截面的SEM照片。由图可知,球形铌粉表面光滑、无毛刺、内部结构致密、未发现明显的孔隙等缺陷,说明等离子体可提供足够的能量使铌粉颗粒表面或整体熔融而实现致密化。粉末长径比接近1:1,具有较高的球形度。
图4所示为铌粉等离子体球化前后的XRD图谱。由图4可知,球化处理前后铌粉衍射峰的位置并没有发生明显变化,其特征衍射峰为(110),(200),(211),(220)和(310),表明铌粉为体心立方结构。球化前后均呈现单一的Nb相,没有出现其它杂质相的特征衍射峰。采用氩气作为等离子体工作气,经射频等离子体球化处理后可以制备单相铌粉。
图5所示为3种不同粒度的铌粉球化前后的激光粒度分布图。如图5(a)所示,原料铌粉的平均粒度为24.83μm,经等离子体球化处理后,平均粒度变为25.07μm。可见球化前后的铌粉平均粒度改变很小,但粒度分布曲线变窄,粒度分布更加集中。这主要是由于粉体在穿过等离子体高温区时,细微颗粒(<5μm)迅速熔化为液滴,且飞行速度快,在表面张力作用下,与相碰撞的表面熔化的粗大粒子合并,形成球形颗粒,过于微小的颗粒被快速汽化,随气流进入除尘布袋装置,所以在图中表现为原粉的最小颗粒在球化后不见了。图5(b)、(c)表现出相同的变化规律。
2.2 加料速率对粉体球化率的影响
在射频等离子体球化处理过程中,工艺参数尤其是加料速率对铌粉的球化有重要影响。在相同工艺参数下,不同的加料速率,粉末的球化效果不同。图6所示为以粒径24.83μm的铌粉为原料,在不同加料速率下制备的球形铌粉形貌的SEM照片。由图可知,随加料速率增加,铌粉的球化率降低。这是因为加料速率增加,使单位时间内通过等离子体的粉末增多,粉末完成球化所需要的能量增加。而系统在固定的工艺条件下所能提供的能量为有限的定值,不能满足过量铌粉的吸热、熔化和球化的需要,致使粉末的球化率降低。此外,单位时间内进入等离子体炬中的粉末增多,颗粒与发生器中流场的相互作用更加剧烈,造成颗粒运动轨迹杂乱,部分颗粒未能穿过高温区也是造成球化率降低的原因。图7所示为送粉速率15g/min时,铌粉球化处理后的非球形颗粒的SEM照片。从图中可以明显看到:颗粒1、2为典型的吸收能量不足引起的球化不完全,颗粒3表面粗糙,形状不规则,基本保持原粉的形貌,是由于流场作用下杂乱的飞行轨迹使其未能穿过高温区。同时可观察到由于能量不足致使周围部分球形颗粒表面出现不同程度的缺陷。
图8所示为不同加料速率时铌粉的球化率曲线。由图8可知,当送粉速率为2g/min和5g/min时,铌粉的球化率分别可达到100%和97%,当送粉速率增加到10g/min时,球化率下降到85%,进一步加快送粉速率到15g/min,球化率急剧下降到65%。因此送粉速率为2~5g/min时可获得较高的球化率。
2.3 球化处理对粉体特性的影响
对平均粒径为24.83μm的铌粉球化处理前后的松装密度、振实密度及流动性进行测试,结果如表2。由表可见经射频等离子体球化处理后,铌粉的松装密度由1.33g/cm3提高到4.35g/cm3,振实密度由1.95g/cm3提高到5.61g/cm3,这是由于球化后球形粉末颗粒堆积时接触面小,粒子间的空隙少,架桥现象明显减少,使松装密度和振实密度得到显著改善。同时,粉末流动性得到明显改善,原料粉末由于粒度细小,粉末之间的范德华力较强,存在粉末团聚现象,粉末不容易流动;且粉末形状为不规则的块状体,架桥现象严重,导致微细铌粉流动性变差。球化处理后,架桥现象清除,流动性得到改善,达到12.51s/(50g)。可见,经射频等离子体球化处理后,铌粉的粉体特性得到很好的改善,适于注射成形及凝胶注模成形等粉末冶金工艺。另外,由表2可知,球化处理后粉末的收集率约为28.3%,收粉率不高是目前等离子体制粉技术遇到的普遍问题。主要是由于颗粒在等离子体流场中受到自身重力、气流拖拽力以及电磁场的影响,运动轨迹紊乱,穿过等离子体炬高温区后部分液滴黏在冷却室内壁并冷凝沉积,还有部分小液滴汽化后随尾气进入除尘装置,造成粉末总量减少。
3 结论
1)采用射频等离子体系统制得单相、球形铌粉。制备的球形铌粉表面光滑、分散性良好、球形度高,加料速率为2g/min时,球化率可达100%。球化处理后粉末粒度分布变窄。
2)加料速率对粉末的球化率影响较大。随加料速率的增加,铌粉的球化率逐渐降低。加料速率在2~5g/min时可以获得较高的球化率。
3)球化处理后铌粉的松装密度、振实密度和粉末流动性得到明显改善。松装密度由1.33g/cm3提高到4.35g/cm3,振实密度由1.95g/cm3提高到5.61g/cm3。流动性提高,达到12.51s/(50g)。
参考文献:中图分类号:TF123 文献标识码:A 文章编号:1673-0224(2014)3-361-06
星尘科技(广东)有限公司专注于高性能金属粉末材料的研发与生产,球形铌粉采用射频等离子体球化制粉技术制备,具有高纯度(≥99.95%)、低氧含量及优异球形度(流动性≤15s/50g),适配电子束熔融(EBM)等金属增材制造工艺。该材料凭借铌的耐高温、耐腐蚀特性,可应用于航空航天高温部件、超导材料及半导体设备关键组件等领域。公司依托广东省新材料研究所科研团队,通过粒径分级与表面改性技术实现粉体性能定制化,已为国内多家科研院所及高端制造企业提供稳定材料解决方案。如有稀有难熔金属粉末的需求,欢迎联系我们的专业人员,郑经理13318326187.