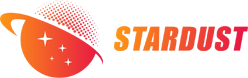
金属钨具有高密度、高熔点、高强度、低的热膨胀系数、良好的抗腐蚀性能和热电子发射能力等优良性能,在航空航天、军事工业和电子工业等许多工业和国防领域都得到了广泛应用[1-5]。球形钨粉具有良好的流动性和高的松装密度,在工业生产中已受到越来越广泛的关注。在热喷涂领域,球形钨粉因其具有良好的流动性,制备的涂层更加均匀、致密,且有良好的耐磨性[6,7]。此外,用球形钨粉制备的多孔钨阴极材料具有更均匀的孔隙,将取代常规的钨粉用于多孔钨部件的制备[8]。在粉末冶金领域,球形钨粉具有高的松装密度,在烧结过程中收缩非常均匀,可实现良好的尺寸控制[9]。
射频等离子体具有温度高(约104℃)、等离子体炬体积大、能量密度高、传热和冷却速度快等优点,是制备组分均匀、球形度高、缺陷少、流动性好的球形粉末的良好途径[10-12]。以等离子体为热源,在难熔金属球化处理方面具有较大的技术优势[13]。射频(RF)等离子体在球化处理粉末的过程中,其高温提供的足够能量使粉末在穿越等离子体时迅速吸热、熔融,并在表面张力作用下缩聚成球形,在极短的时间内骤冷凝固,从而形成球形的粉末。等离子熔融球化技术被认为是获得致密、规则球形粉末的最有效手段之一。
本实验以不同粒度、不规则形状的钨粉为原料,通过射频等离子体球化处理制备球形钨粉。主要针对制备球形钨粉的工艺进行研究,并着重对加料速率对粉末球化率的影响进行了分析。
1 实验
实验采用费氏粒度为5.5,11.5,26.5μm的钨粉为原料,粉末形状为不规则形。用于制备球形钨粉的射频等离子体装置,主要包括射频感应等离子发生系统,频率为3.5MHz,额定功率为100kW;冷却室,喂料系统和产品收集系统,如图1所示。
该装置以氩气为工作气体建立稳定运行等离子体炬,并以氩气作为载气将钨粉经喂料系统、加料枪轴向送入等离子弧中,粉末进入等离子体的位置位于感应线圈的第二圈。在等离子体球化处理过程中,粉末颗粒穿过等离子体高温区瞬间吸热、熔融、球化,然后进入冷却室迅速冷凝形成球形钨粉,经收集系统得到球形粉末,详细工艺参数列于表1。
采用日本理学公司的D/MAXRB型X射线衍射仪进行相组成检测;采用LEO-1450型扫描电镜对粉末进行形貌和显微组织观察;粉末的粒度和粒度分布采用日本清新公司的LMS-30型激光粒度分析仪进行测试;采用霍尔流量计测定钨粉的松装密度和流动性。
2 结果与讨论
2.1 不规则钨粉的等离子体球化
图2为粒度5.5μm(图2a1,b1)、11.5μm(图2a2,b2)和26.5μm(图2a3,b3)不规则形状钨粉射频等离子球化处理前后的SEM照片。由图2可以看出,钨粉经等离子体球化处理后得到表面光滑、球形度高的钨粉(如图2b1,b2,b3所示)。且粉末分散性良好,团聚现象消失,球化率可达100%。
实验中发现,球化处理后的粉末中含有异常长大的大球形钨粉。图3为球化处理前后钨粉的激光粒度分布。由图可知,原料钨粉的平均粒度为19.36μm,且80%的粉末粒度分布在10~35μm之间。等离子体球化处理后,平均粒度为33.59μm,粒度增大。由于原料粉末存在团聚现象,而团聚粉末在球化处理过程中未充分分散,造成其整体熔融、球化,形成大颗粒的球形钨粉。此外,在等离子体球化过程中,由于部分粉末运行轨迹的紊乱,熔融的钨粉在穿越等离子体时相互碰撞,形成大颗粒的钨粉(如图4所示)。
图5为球形钨粉(26.5μm)截面的SEM照片。由图可知,原钨粉的不规则形状的棱角已消除。球形钨粉的内部结构致密,说明粉末在等离子体球化处理过程中充分吸热,表面或整体熔融,实现粉末的致密化。球形粉末长径比接近1:1,粉末的球形度良好,为规则的球形。
射频等离子处理前后钨粉的XRD图谱如图6所示。由XRD图谱可知,球化后的钨粉衍射峰的位置与原料钨粉一样,并没有发生变化,其特征衍射峰(110),(200),(211)和(220)表征粉末为体心立方(bcc)结构。球化前后都呈单一的W相,没有出现其它杂质相的特征衍射峰。采用氩气作为等离子体工作气,经射频等离子体球化处理后可以制备单相钨粉。
2.2 加料速率和粉末粒度对粉末球化率的影响
在射频等离子球化处理过程中,工艺参数尤其是加料速率对钨粉的球化有重要影响。在相同工艺参数下,不同的加料速率,粉末的球化效果不同。图7为加料速率对粉末球化率的影响。由图7可知,不同粒度的钨粉,随着加料速率的增加,粉末的球化率降低。当加料速率大于25g/min时,粉末的球化率明显降低。由于加料速率的增加,单位时间内通过等离子体的粉末增多,粉末球化所需要的热量增加。然而,系统在固定的工艺条件下提供的热量为定值,不能满足过量钨粉的吸热、熔融和球化的需要,致使粉末的球化率降低。此外,加料速率的增加,导致部分粉末在等离子体中的运行轨迹偏离等离子体高温区,粉末吸热不充分,最终导致粉末球化率的降低。在系统一定的工艺条件下,合理的加料速率是保证粉末球化率的重要因素。
从图7还可以看出,当加料速率一定时,球化率随粉末的粒度增加而降低。粒度较小的粉末,其比表面积较大,穿越等离子体时吸收热量更充分,有利于粉末的球化。一般来说,随着粉末粒度的减小,其熔点也降低,吸收同样的能量更容易球化。因此,相同的工艺参数下,较小粒度的粉末球化率更高。
图8给出了26.5μm钨粉不同加料速率制备球化粉末的SEM照片。由图可知,当加料速率为5g/min(图8a)和10g/min(图8b)时,钨粉的球化率达到95%以上。当加料速率增加到15g/min(图8c)和20g/min(图8d)时,钨粉的球化率仍能保持在80%以上,其中15g/min的球化率为90%。当加料速率增加至25g/min(图8e)和30g/min(图8f)时,钨粉的球化率分别为70%和50%。
2.3 球化前后钨粉的松装密度和流动性
图9为26.5μm钨粉球化率对粉末松装密度和流动性的影响。由图可知,随着钨粉球化率的提高,松装密度也逐渐得到提高,粉末流动性得到很大改善。当钨粉的球化率从0增加到100%时,粉末的松装密度由原料粉末的6.80g/cm3增加到11.5g/cm3,粉末流动性由14.12s/50g提高到6.95s/50g。
影响粉末松装密度的主要因素是颗粒的形貌。球形颗粒堆积时接触面小,架桥现象减少,粒子间的空隙少,有利于堆积密度的提高。粉末球形度越高,松装密度越大。因此,球形钨粉具有高的松装密度。粉末的流动性与形貌和粒度有直接关系。粉末的形貌越规则、越光滑,粉末接触面积越小,摩擦力越低,粉末的流动性越高。球化处理后,钨粉形状变为规则的球形,利于粉末松装密度的提高和流动性的改善。
3 结论
1)通过射频等离子体处理技术可以得到单相球形钨粉。球形钨粉表面光滑、球形度好,球化率可达100%。球化处理后,钨粉粒度略微增加。
2)加料速率是影响粉末球化率的重要因素。在相同工艺参数下,随着加料速率的增加,钨粉的球化率降低。粒度较小的钨粉的球化率较高。
3)随着钨粉的球化率提高,粉末的松装密度和流动性得到改善。钨粉的松装密度由6.80g/cm3提高到11.5g/cm3,粉末流动性由14.12s/50g提高为6.95s/50g。
参考文献:稀有金属材料与工程,第40卷第11期,射频等离子体制备球形钨粉的研究
星尘科技采用射频等离子体球化技术制备的球形钨粉,具有高纯、低氧、球形度高、表面光滑、无卫星球、极少空心颗粒、粒度分布均匀,具有优异的流动性能以及高的松装密度和振实密度。钨具有优异的耐高温和射线屏蔽性能,也广泛应用于国防工业、医疗设备等领域。球形钨粉适用于激光/电子束增材制造、激光直接沉积、热等静压、注塑、激光熔覆等工艺。
详情请联系我们的专业人员:郑经理13318326187