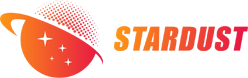
0 引 言
钼属于 VIB 族元素,原子序数42,相对原子质量95. 95,核外电子排布[Kr]4d5 5s1,电离能7. 5 eV,相对密度10. 2 g/cm3 ,熔点2622 , 比热0. 28 J/(g ·K) ,热导率142.1W/(m ·K) ,热膨胀系数5.3×10-6/K,钼具有体心立方结构,具有较明显的塑-脆变温度。随着光电子学与薄膜技术不断发展,高纯钼因其高熔点(2625℃)、高导热导电率、良好的耐腐蚀性、低比阻抗、良好的抗热震和抗热疲劳性质、好的韧性和延展性、中等硬度等特点,作为钼靶材通过溅射沉积在各类基材表面形成溅射膜,广泛应用于各种电子产品。如耐高压大电流半导体器件的钼引线、声像设备、照相机零件、高密度集成电路中的门电极、高精密电子工业的薄膜晶体管液晶显示器( TFT-LCD)和新型薄膜太阳能电池等。另外,高纯钼还可用于火箭喷嘴、催化剂、化学试剂等。
钼的电子特性很大程度上取决于它的纯度,其纯度直接影响应用。例如:平面显示领域和太阳能电池领域对原料钼粉纯度要求质量分数达到99.99%(4N)以上,集成电路领域用高纯钼粉纯度要求达到99.999%(5N)以上。在电子行业中,碱性金属元素Na和K等离子容易在绝缘层中产生漂移,影响其导电性能;放射性元素铀(U)和钍(Th)等元素会释放天然的α射线造成器件软击穿。Fe、Ni等元素影响薄膜成型,从而产生界面漏电;气体元素,如O元素影响薄膜的电阻率[1-2],非金属元素S、C等,在高温环境中易与钼形成MoC等导致高纯钼发生磨损开裂。因此,必须严格去除这些有害的杂质元素,提高作为原料的钼金属纯度,从而保证电子行业所需的高精度以及大的均匀性。
目前,工业化大批量生产的钼粉纯度为99.95%,远达不到微电子行业的要求,之前对于高纯钼粉的报道主要集中在日本东京钨公司、东芝公司、日立公司,德国的斯达克公司和奥地利Plansee等,日本东芝公司以φ100μm二钼酸铵为原料,通过氢还原得到普通钼粉,通入过氧化氢将钼粉氧化溶解为钼酸溶液,然后用阳离子交换树脂提纯,烘干得到高纯三氧化钼,粉碎至5~20μm,最终采用特制的钼层内衬还原设备氢还原制得5N~5N5的高纯钼粉[3],流程图见图1。
德国H.C.Starck公司采用运动床以二钼酸铵为前驱体制出粒度为2.3μm的钼粉[4],经压制烧结再加工得到纯度为5N的高纯钼粉。德国柏林赫尔曼·斯达克公司采用特制设备在10级绝对清洁室成功将钼粉纯度提高到6N以上,目前该生产线的年生产能力为2.5t。奥地利Plansee生产的钼粉纯度为99.97%(计钨),其生产的钼溅射靶材纯度能达到4N。中国作为最主要的钼储量国和生产国,虽然钼资源丰富,但主要生产钼中初级产品,高附加值产品少,占全球钼行业利润份额低。国内目前也有大批研究者在做高纯钼相关工作,中南大学赵中伟院士团队研发出纯度可达到99.995%(4N5)(计钨含量)的高纯钼粉,可进行实验室公斤级生产,目前正在进行产业化试验。金堆城钼业股份有限公司金属分公司2023年已实现年产4N钼粉1000t。近年来,我国制备高纯钼已取得了长足进步,但仍然缺乏系统性研究。
本文介绍了高纯钼粉现有的制备技术,指出了目前研究中存在的一些问题,并分析了其应用前景。
1高纯钼粉的制备技术
目前,生产高纯钼金属[5]的主要方法有:(1)提高制备钼金属的原料—钼化合物的纯度。例如:高纯钼酸铵或高纯MoO3通过高纯氢还原或碳还原得到高纯钼粉;高纯MoCl5通过氢等离子焰还原或水解,干燥制得MoO3再还原得到高纯钼粉;高纯Mo(CO)6蒸汽热分解得到高纯钼等。(2)普通钼粉经处理纯化制备高纯钼。主要方法包括:电子束熔炼、等离子球化等。
1.1提高制备钼金属的原料—钼化合物的纯度
1.1.1高纯MoO3还原法
制备高纯钼的原料一般为二钼酸铵(ADM)或四钼酸铵(AQM),分子式为(NH4)2Mo2O7、(NH4)2Mo4O13。首先,钼酸铵加热焙烧失去结晶水,氨挥发,得到MoO3,然后氢气条件下还原或碳还原MoO3,水蒸气或CO2挥发得到金属钼粉。图2为二钼酸铵、三氧化钼及钼粉的形貌图。其制备化学方程式如式(1)~(4)所示。
因此,高纯钼制备的首要条件是提纯得到高纯钼酸铵或高纯MoO3。而提纯钼酸铵或MoO3的方法包括升华法、沉淀法、溶剂萃取法、离子交换法、结晶法等。
升华法:利用MoO3在600℃以上显著升华的特点生产纯的MoO3。升华温度在600-1000℃,MoO3纯度可达到3N5以上。如温度过高,原料中杂质也会被升华蒸发而进入MoO3中[6]。美国Climax公司最早用升华法生产纯三氧化钼,该公司Moiseev等[7]研制出一种新型升华炉,首先将氧化钼置入升华炉,在一定真空度、550-580℃条件下,升华出氧化钼粉中易挥发的化合物如氧化硒、氧化锑、二氧化硫和MoO3颗粒上的吸附水和化学结晶水;然后在690-780℃、一定真空度下升华MoO3,升华后的MoO3冷却至500-550℃,收集制成纯MoO3,为淡绿色针状晶体,纯度可达到4N5。升华法工艺最简单,二十世纪五六十年代在欧美广泛使用,但因该法生产的氧化钼纯度波动较大,无法标准化生产,而且物理性能有较多缺陷,目前已被淘汰。
沉淀法:根据钼与杂质的性质不同,加入不同沉淀剂,使钼与杂质离子分离的方法。例如硫化沉淀法除铜、铁、铅等;镁盐沉淀法除磷、砷、硅等[8-9];铁盐沉淀法除钨等。杨亮等采用铵镁盐沉淀法使钼酸铵溶液中的砷形成砷酸铵镁沉淀而除去。在氯化镁用量为理论量的1.2倍、室温、反应时间30min条件下,钼酸铵溶液中的砷质量浓度下降至1/170,多余的Mg2+用724弱酸性阳离子树脂吸附除去,除砷反应式如式(5)~(6)所示。
钨钼同属于ⅥB族元素,由于镧系收缩的影响,钨钼的离子半径非常接近,原子结构及化学性质相似,钨钼深度分离是目前粉末冶金学难点之一。冷明峰等[10]采用吸附共沉淀法,可针对氨浸法生产的钼酸铵溶液除少量钨,具体方案是溶液中加入Fe(NO)3·9H2O,以新生态Fe(OH)3为载体共沉淀钨,在pH=7.5~8.5、Fe3+/W质量浓度比为6、陈化时间为24h时,W的吸附分离效果最佳。与萃取法和离子交换法相比,沉淀法操作简单,工艺流程短,生产成本低,但深度除杂效果不明显,工业上适用于原始料液的初步提纯。
溶剂萃取法:利用化合物在两种互不相溶的溶剂中分配系数的不同,使化合物从一种溶剂中转移到另一种溶剂中。溶剂萃取法在制备高纯钼酸铵过程中,主要采用胺类萃取剂,图3为萃取法提纯钼酸铵生产高纯钼粉流程图。Viktor等[11]采用萃取法净化提纯制备七钼酸铵,将工业三氧化钼碱浸得到的粗钼酸钠溶液,调节pH至2.5,用含双十三胺的有机相萃钼,将负载钼有机相引入搅拌器中,加入氨水和上批次冷却结晶的母液,调节氨钼比至1.2∶1,反萃得到含钼量19.24%的反萃液,然后在15~20℃条件下冷却结晶得到七钼酸铵。俞克宁等[12]在高钼低钨弱碱性溶液中,加入硫酸控制平衡水相pH=78,此时钨以单聚体WO-形式存在溶液中,使用伯胺1%~2%N1923作为萃取剂,煤油作为稀释剂,伯胺通过氢键形成分子缔合物的溶剂化萃取机理优先萃取钨,生成RNH2·H2WO4,实现从钼酸盐溶液中微量钨的去除。宁朋歌等[13]针对俞克宁的试验进行了补充研究,发现伯胺对处理高钨低钼溶液效果不大,但有利于处理高钼低钨及浓度相当的钨钼溶液,溶液中W/Mo越小越有利于钨钼分离,但绝对过量的钼也会抑制钨的萃取,当50g/L钼和1.0g/L钨混合溶液,萃取剂为复合胺(体积比1.5%伯胺N1923,0.5%仲胺7207)+羟肟(1%的羟肟BK992或Lix984)+稀释剂(煤油),控制萃余液pH为7.09,两级萃取,然后用10%的氢氧化钠溶液反萃,钨钼分离系数达到105。张贵清等[14]以10%的季铵盐N263为萃取剂,20%仲辛醇作为极性改善剂,70%磺化煤油作为稀释剂,将3者混合作为有机相,与碱性粗钼酸钠溶液按一定相比进行多级逆流萃取,钼萃入有机相,杂质磷、砷、硅等随萃余液排放。负载有机相经去离子水洗涤后采用碳酸铵溶液多级逆流反萃,得到纯度较高的钼酸铵溶液。萃取法因其平衡速度快、分离效果好、处理量大、操作易连续自动化、安全方便等优点而在稀有金属工业得到了普遍的应用。但是萃取剂为有机溶剂,有一定的毒性,环保压力大,处理困难。
离子交换法:在一定pH值下,利用钼酸根离子与杂质离子在离子交换树脂上的吸附能力不同而将两者分离的方法。根据离子交换树脂上的可交换离子,将其分为阳离子交换树脂、阴离子交换树脂及氧化还原树脂,阳离子交换树脂的官能团是各种有机酸,根据有机酸酸性强弱,可将其分为强酸型、弱酸型阳离子交换树脂,酸以H+与其他阳离子进行交换反应。阴离子交换树脂的官能团是各种胺类,其中,强碱性树脂功能基为季胺盐,弱碱性树脂功能基为伯胺、仲胺、叔胺。阴离子交换树脂自身都具有很强的碱性,易于加和H+而带正电荷,从而可以结合一个阴离子(OH-型或Cl-型),结合的阴离子与钼酸根等阴离子进行交换反应。氧化还原树脂是溶液中的离子与树脂上的功能基发生氧化还原反应,从而与其他物质分离。图4为离子交换法提纯钼酸铵生产高纯钼粉流程图。日本东芝公司改进之前的方法,将普通钼粉置于聚四氟乙烯容器中加水搅拌[3],然后加入30%的双氧水氧化,得到钼酸溶液,经H型阳离子交换树脂除杂,蒸发浓缩结晶,烘干得到高纯MoO3。2016年,宋爱谋等[15]以仲钼酸铵为原料,加入硝酸铁吸附、陈化,过滤掉不溶杂质,然后过D380离子交换柱进一步除杂,再加硝酸,酸沉得到多钼酸铵沉淀,煅烧得到高纯MoO3,再通过氢还原得到4N~5N的钼粉,粒度0.5~10μm。2018年,高观金等[16]采用连续循环离子交换法提纯工艺和高纯氢气还原脱钾技术,以99.95%的仲钼酸铵为原料,离子交换法除钾和钨,回转炉自动化焙烧得高纯MoO3,分两次还原,一次自动化还原得MoO2,二次还原过程中掺杂挥发性材料进一步辅助钼粉中K的挥发,真空包装,生产过程中采用一体成型料筒用于周转,得到4N钼粉。2020年,操齐高等[17]将仲钼酸铵通过离子交换纯化,然后调节pH=1,进行气流式雾化,得到仲钼酸铵粉末,再通过5N超纯氢还原,得到4N球形钼粉,平均粒径3.5μm。离子交换法在提纯钼酸铵制备高纯钼过程中,虽然水资源耗费较大,部分树脂吸附交换能力低,但其较沉淀法、结晶法等一般的分离方法提纯效果好,产品纯度高,且树脂种类多,可选择范围宽,其分离选择性好,富集比高,自动化程度高,产品性质稳定,树脂再生后可重复利用,工艺安全环保,是未来工业生产高纯钼粉原料的必然选择。
结晶法:将目标物质从溶液中析出的一种方法。钼酸铵结晶包括加热蒸发溶剂的蒸发结晶、降低饱和溶液温度的冷却结晶以及加酸沉淀的酸沉结晶。结晶可使目标物质得到纯化,但想要获得较好的纯化效果,往往需要多次重结晶。在结晶过程中,钼酸铵溶液中大多数阳离子杂质包括Fe2+、Cu2+、Mg2+、Ca2+、K+、Na+以及阴离子杂质Cl-、SO-、NO3-均留在溶液中,钼酸铵得到纯化。一般情况下将钼酸铵多次重结晶,提纯、焙烧可得到高纯MoO3。2022年郭蔚等[1]以99.95%仲钼酸铵为原料,焙烧得MoO3,氨浸得到钼酸铵溶液,两级过滤,蒸发结晶,得到的仲钼酸铵再重复一遍上述步骤。经两次提纯,焙烧得超高纯MoO3,5N氢气还原制得大规模集成电路用5N超高纯钼粉。郭超等[18]利用钨钼同多酸及其杂多酸性质的差异,在不同工艺条件下对钼酸铵进行酸沉结晶分离钨钼,控制酸沉终点pH值为2.5,酸沉前加入磷酸铵可使钨和钼结晶率有较大差异,尤其当钨钼比较大时,分离效果好。因原矿中钾含量较高,金钼股份在生产实践中,采用多次硝酸酸沉结晶,将钾含量有效降低至≤8×10-6,制得的低钾钼酸铵为制备高纯钼酸铵奠定了良好的基础[19]。酸沉结晶法过程中消耗大量无机酸,二次投入成本大,且易造成环境污染,但降钾效果较好,在目前尚无更好的降钾工艺之前,可优先使用。
高纯 MoO3 还原法是目前制备高纯钼粉使用最广泛的方法,在高纯MoO3氢还原或碳还原制备高纯钼粉的过程中,必须严格保证环境纯净度。2007年,汪涛等[20]用高纯氢气还原高纯钼酸盐或钼氧化物,采用纯度≥98%的纯钼舟皿,制得4N的高纯电子级钼粉,氧含量低于0.1×10-6。2022年,唐鑫鑫等[21]以99.95%MoO3为原料,采用4N氢气还原,过0.18mm筛得MoO2,喷去离子水,干燥,再进行二次还原,过0.075mm筛,得到炉前钼粉。然后采用流化床气流分级机进行分级,按粒度取中间第二级,得到粒度3-5μm、纯度3N8的钼粉,该还原过程采用纯钼或表面喷涂钼涂层的耐高温舟皿。2023年,任宝江等[22]将低钾MoO3在马弗炉中一段还原得到MoO2,为降低Fe、Ni的引入,在十八管炉中使用钼镧合金舟中进行二段还原,控制还原温度和氢气流量,然后进行清洁化筛分、混料、包装得4N钼粉,其中十八管炉可有效除钾,钼镧合金舟可进一步降低Fe、Ni、Cr等杂质,产品K含量≤20×10-6,Fe+Ni含量≤10×10-6,W含量≤50×10-6,该工艺可工业化批量生产。2020年,张国华等[23]将钼酸铵或高纯MoO3与炭黑按1∶0.5-1∶2比例混合,400-750℃惰性气氛焙烧,得到含一定量炭黑的超细MoO2,然后在800-1150℃下再焙烧得到含有一定纳米钼核心的MoO2,最后在600-1100℃下进行超纯氢还原得到高纯纳米钼粉,平均粒度40~200nm,C含量≤0.01%。该方法成本低、工艺简单、高效、是大规模工业化生产纳米钼粉的好办法,但未公布具体纯度指标。
1.1.2氯化物MoCl5分解法
获得高纯卤化物的工艺原理是:将工业三氧化钼卤化得到卤化物(一般为MoCl5),然后在550℃分馏处理,使里面的杂质挥发,得到5N卤化钼,最后通过氢等离子焰还原或水解,制得高纯钼粉。吴秋生等[24]将钼粉通氩气混合除氧,然后通Cl2并控制流量,加热至600-700℃反应,随后冷却得到MoCl5粉末,经提纯得到高纯MoCl5。日本东芝株式会社将MoO2与卤素反应生成金属卤化物,再将所制得的卤化物加水分解得到MoO3,将MoO3还原得到4N钼粉。2012年,谭兴龙等[25]改进了上述方法,将MoO2粉末与Cl2在220-500℃反应50~240min,冷却得到MoO2Cl2固体,该反应为选择性反应,其他元素几乎不参加反应。然后氨浸、焙烧,得到高纯MoO3,再经高纯氢还原制得高纯钼粉,纯度可达到5N,甚至5N5以上。化学反应式如式(7)-(9)所示。MoCl5、MoO2Cl2与湿空气接触均会分解产生HCl气体,有腐蚀性和毒性,对设备造成不可逆的腐蚀,同时影响产品质量。Cl2有强烈毒性,在生产过程中不好控制,因此金属氯化物分解法制备高纯钼粉未能得到工业化应用。
MoCl5还可通过氯化物熔盐电解法[6]制备金属钼,熔盐电解法是应用电化学原理,利用电能将某些金属盐类熔融并作为电解质进行电解从而生产高纯金属的方法,目前已成为工业上生产碱金属、稀土金属、稀土合金等金属的一种重要方法。以石墨为阳极、金属钼为阴极,采用氯化物熔盐电解法,将氯化钼作为原料装入电解炉中,由于离子电极电位不同,钼阳离子在电解槽阴极获得电子还原成金属钼,可除去金属杂质和大多数非金属杂质,产品为纯度99.95%的树枝状钼粉。该方法具有设备简单、易操作、易实现生产连续化等优点,但生产的钼粉纯度已不满足现在电子行业的需求,还需不断改进。
1.1.3羰基钼Mo(CO)6热分解法
羰基钼热分解法[26]是以羰基钼为原料,在常压、350-1000℃、N2气氛下,进行蒸汽热分解处理。它利用了羰基化合物的分解,在气相状态下形核、结晶及晶核长大,制备的钼粉平均粒度24μm,随着热解温度的升高,钼粉粒度下降。为了更好地降低碳含量,先在石英管炉通空气在400-500℃下使羰基钼氧化,然后在700-800℃纯净氢气条件下还原得到金属钼粉。化学反应式如式(10)所示,利用该法制得的钼粉具有很高的化学纯度和良好的烧结性,而且此方法可用于工业化,但原料不易得。
1.1. 4 其 他
2023年,高志强等[27]采用4N5的MoS3在回转炉中通4N的H2和N2还原,尾气从进料端负压抽走,可制得4N钼粉。化学反应式如式(11)、(12)所示,该法对原料纯度要求高,不适合大规模生产。
1.2普通钼粉经处理纯化制备高纯钼粉1.2.1电子束熔炼法
电子束熔炼[6]是利用高速运动着的电子流轰击金属钼,电子束的全部动能转变成热能,使熔池内温度可达3000~3200℃,金属钼熔化,低熔点、高饱和蒸气压的杂质在熔化过程中被真空抽走,熔炼时熔池能较长时间处于高真空状态下,金属钼可获得最佳净化效果。一次电子束熔炼杂质可降低至少80%,可以采用多次熔炼以满足高纯钼的需求。图5为电子束熔炼的过程示意图。该方法已被应用于提纯多种材料,例如钨、钽、钛、镍、铱等。日本一家金属公司采用电子束精炼方法制成了一种高纯度钼材,其纯度可达到6N[28]。其金属杂质和气体杂质数量较低,而且具有容易锻造、轧制和焊接等优点,比采用粉末冶金方法生产的钼材具有更重要和更广泛的用途。
1.2.2等离子球化法[6,29]
感应等离子球化法是将普通钼粉颗粒由送粉气体氢气携带进入等离子体炬(等离子体中心区温度高达10000℃以上)中,使之迅速熔融气化、裂解,熔融的颗粒在表面张力的作用下形成球形度很高的液滴,并在极短的时间内迅速冷凝,从而制得高纯致密球形钼粉。该方法具有产品分散性好、球形度高、反应气氛可控等特点,并且整个制备过程速度快,可实现连续化生产。图6为感应等离子体实验装置示意图,该方法对设备要求非常高,工业化生产投入比较高。2017年,刘金涛等[30]在99.9%的钼粉中加入粘结剂和去离子水制成料浆,喷雾造粒,干燥得到钼粉团聚体,然后脱胶、排杂,在H2气氛下烧结得造粒钼粉,氩气保护下筛分,再进行等离子球化得到熔融钼粉,在小于30℃下急冷固化,得到高纯致密球形钼粉,纯度为4N,粒径30~40μm,松装密度6.0g/cm3。图7为等离子球化钼粉形貌图。
目前制备高纯钼粉最常用的方法仍然是在生产前端提纯钼化合物。高纯钼酸铵或高纯MoO3通过清洁化焙烧及还原得到高纯钼粉。在制备过程中,需要保证环境纯度。例如在超净车间进行、采用一体成型装料桶、采用纯钼制或者钼涂层舟皿、工艺过程中使用高纯气体等。该方法成本相对较低且可操作性强,易进行工业化生产。电子束精炼法可通过多次精炼制备纯度极高的钼粉,但电子束精炼法和等离子球化法成本较高且对原料钼粉的纯度要求较高。在生产过程中往往需要采用多种提纯方法有机结合以达到更好的净化效果,实现高纯钼粉的制备。
2高纯钼粉应用前景
在国防领域,金属钼及其合金因熔点高且能抗高温热粒子流的冲刷成为固体燃料火箭发动机的最佳选用材料,主要用做燃气舵片、隔热屏、动力喷管及各种紧固件等耐高温部件。核聚变反应堆第一壁材料需要在超高温强热载荷条件下工作,而金属钼热稳定性好、抗热震性良好,能在高热载荷环境下工作,同时其氢同位素留存量低,侵蚀速度慢,故成为代替C-C复合材料等低Z材料的新型核聚变实验反应堆的等离子体表面及结构材料,金属钼克服了低Z材料氚留存量多及中子照射使其热导率变坏等缺点。在冶金与机械工业领域,钼元素作为合金钢添加剂可有效提高钢的淬透性和回火稳定性,同时细化晶粒、提高碳化物的分布均匀性,进一步提高钢的强度和韧性。钼顶头因其高温强度大,可承受不锈钢变形产生的应力,且不需要冷却水降低顶头温度,管壁内外温度梯度小。同时,1支钼顶头可穿制300根以上的管坯,远远超过水冷顶头(1支只能穿制1根不锈钢管坯),经济效益最佳。钼金属因其比钨更易加工制造,常用作1350℃以上使用的真空或惰性气体保护的高温、炉发热体。在玻璃熔炉中,钼耐高温抗熔融玻璃腐蚀,即使微量腐蚀,其氧化腐蚀产物MoO3易挥发,不会污染玻璃,因此常用作玻璃电熔窑的供电电极。钼因其耐高温且能在收到电子束轰击时原位产生X射线,可用作X射线管的旋转阳极靶,检验材料的内部结构和人体的病灶。钼材料还可用作溅射靶,通过各种溅射技术、化学气相沉积、物理气相沉积等方法在构件表面施加一层钼薄层以改善构件表面性能。
近年来,电子行业的精细化发展对钼金属提出了更高的要求,同时钼金属新性能的发现又促进了电子行业的发展,两者互相成就。研究钼金属的本征性能必须进行深度净化,去除其中微量甚至痕量杂质的影响,从而发现其新功能并开拓新的应用。高纯钼粉主要应用于电子行业及高精尖行业,在平面显示、太阳能电池及集成电路中具有非常高的附加值。随着平面显示器的大型化和高精度化,高纯钼(4N)因其较低的比阻抗(Cr的1/2)而代替Cr逐渐成为平面显示领域配线材料的优选。在LCD中,高纯钼的使用还可大大提升液晶显示器的亮度、对比度、色彩以及寿命。在新能源行业中,高纯钼(4N)通过溅射沉积在CIGS薄膜太阳能电池的底部形成电池的背接触,对CIGS薄膜晶体的形成、生长、形貌都有很大的作用。在大规模集成电路领域,由于钼形成的薄膜应力小、高温稳定性好,导电性能良好,使用超高纯钼(5N)作为配线材料成为新趋势。国内高纯钼粉处于研发阶段,开发5N、6N级甚至更高纯度钼粉将补链钼粉类产品,可以打破国外头部钼企业的技术垄断,填补国内内控,实现电子信息领域基础原材料的自主保供,社会效益显著。
3展望
高纯钼在未来科技发展中有着非常广阔的应用前景,而目前国内外市场上仅有的5N、6N钼粉仅处于实验室小试阶段,未实现工业化生产,远远无法满足市场需求。高纯钼粉的研究未来将面临巨大的挑战。首先,原料钼矿来源不同,杂质成分复杂,缺乏一套系统完整的除杂标准,我们亟需针对不同钼原料及杂质成分,根据杂质元素的特点及其与钼之间的差异,建立一套系统完整的纯化技术体系;其次,高纯钼的制备对环境要求非常高,因此需要提高生产环境、所用化学试剂、气体、生产设备以及检测仪器的纯净度;最后,高纯钼制备技术的发展离不开可靠的检测手段,现有的电感耦合等离子体质谱法(ICP-MS)及辉光放点质谱法(GDMS)目前尚可满足生产中相关溶液和高纯金属固体的检测要求,但随着纯度的进一步提高,仍需开发出更低检出限的痕量元素检测技术。开发出低成本、绿色高效的提纯方法,提出更高效的除杂设计方案,制备出纯度更高、质量更稳定的高纯钼材料将是我们未来共同的需求。
星尘科技射频等离子体球化制粉设备制备的球形钼粉,具有纯度高,含氧量低,球度高,表面光滑,无卫星球,极少空心颗粒,粒度分布均匀,流动性能优异,容重和丝锥密度高。广泛应用于接触材料、航空航天耐高温元器件、靶材等领域。球形钼粉适用于激光/电子束增材制造、激光直接沉积、热等静压、注塑、激光熔覆等工艺。
咨询热线:+86 13318326187 郑经理
参考文献:2024年6月第48卷第三期,中国钼业,DOI : 10. 13384/j. cnki. cmi. 1006 - 2602. 2024. 03. 001;
中图分类号:TG142. 71 文献标识码:A 文章编号:1006 - 2602(2024)03 - 0001 - 07