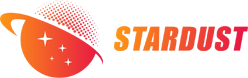
1802年瑞典化学家安德斯·埃克伯格(AndersEkeberg)首次从矿物中提取了73号元素——钽(tantalum),钽的命名源于其在酸中极佳的耐腐蚀性[1]。钽具有比钛更优异的耐腐蚀性[2−4],只受强酸强碱环境影响,在人体内保持相对惰性[5],从而可避免干扰生物组织[1]。通过在模拟体液中形成类似骨骼的磷灰石层,钽被证明具有生物活性并可与骨骼发生生物结合[6]。此外,纯钽及其主要氧化物均具有低的溶解度和毒性[7],自1940年以来就一直在临床上使用,并广泛应用于诊断和植入物,总体效果显著[8]。在骨科、颅面和牙科相关研究中显示出优秀的生物相容性和安全性[9],使用致密钽金属植入物骨整合术已被证明应用时间长达8~12年[10]。
骨科植入物的发展趋势从通过骨水泥、机械固定装置和表面附着等方式固定在骨上,逐渐转变为通过骨整合或骨长入进行生物固定[11−12]。多孔钽植入人体可立即负重并支持骨深入到内部结构,实现良好的长期固定[13],一项长期术后随访研究表明在第11年时多孔钽髋臼假体的存活率为96%[14]。BALLA等[6]研究发现,与多孔钛对照组相比,多孔钽在MTT分析和免疫化学研究方面显示出优异的细胞黏附、生长和分化,多孔钽上形成了丰富的细胞外基质,表面的活细胞密度比钛表面高6倍。WAUTHLE等[15]研究发现,与相同工艺和结构的多孔钛合金相比,多孔钽具有出色的骨传导性能,更高的归一化疲劳强度,并由于其高延展性而允许更多的塑性变形。临床研究表明,随着骨缺损的严重程度和时间的增加,利用多孔钽骨向内生长特性与合适的结构来实现稳定的支撑和结合能力是有效的骨缺损重建方式[16]。多孔钽植入物的优点可概括为:1)材质具有优异的耐腐蚀性能和生物相容性。2)与人体匹配的模量,能有效避免应力屏蔽。3)高表面摩擦特性,可提高初始稳定性。4)足够的机械支撑和较长的疲劳寿命。5)模拟骨的质量传输特性,支持成骨细胞的附着、增殖、分化和矿化,拥有出色的骨整合性能[6,17-18]。
钽作为多孔植入物进行制备时,需通过增加孔隙率使其弹性模量从185GPa降低到3GPa左右从而达到与人骨相似的目的(从小梁骨的0.4GPa到皮质骨的17.9GPa)[19-20]。钽是一种难熔金属材料,熔点高达2996℃,高熔点下钽对氧等间隙元素具有高亲和力,因此实现高孔隙率多孔钽的制备具有一定技术门槛,化学气相沉积(CVD)、粉末冶金(PM)和增材制造(AM)是目前的主要制备技术(见图1[21-23])。CVD是一种工序复杂、成本高的传统制造工艺,具有患者特定解剖特征的多孔钽植入物不容易定制,且多孔结构的设计存在一定限制。PM虽然成本较低,但制备的多孔钽孔隙率较低,孔隙大小不均匀且闭孔率高,内部连通性等问题突出,影响了多孔钽植入物的成骨性能。然而稳定可控且连通性高的多孔结构,正是实现细胞迁移、黏附和增殖的重要因素。因此,利用增材制造技术制备的多孔钽具有孔结构可控且可设计,适合应用于个性化精准医疗之中,尤其是创伤或肿瘤切除引起的复杂骨缺损情形。一直以来,学者们认为钽的应用受到加工技术而非生物性能的限制[6,8,24],相对较高的制造成本和质量控制难度限制了多孔钽的广泛接受度,新兴的金属增材制造正逐步解除这种限制,且允许更灵活、自由地设计多孔钽植入物外形尺寸、内部多孔结构与性能,大大推动了钽金属生物医用材料的应用。
图 1 多孔钽植入物主要制备技术
在多孔钽植入物的增材制造工艺过程中,从模型设计、原材料、设备到成形工艺和后处理均会影响多孔钽质量,相关的监管科学与共性技术研究工作迫切需要协同推进。作者团队结合实际生产,归纳目前增材制造多孔钽的制备瓶颈和难点主要为:1)在原材料方面,医用球形钽粉成本高、可回收次数少,缺乏直接影响增材制造多孔钽质量的钽粉关键性能研究和中间性能研究(如铺展性能、湿度)等,系统性验证和控制原材料球形钽粉对增材制造多孔钽理化性能均一性影响的难度和成本高。2)在缺陷形成方面,增材制造过程中极高的冷却速率及非平衡凝固导致多孔钽产生了各种难以控制的缺陷,不同工艺条件和不同间隙杂质元素水平诱导形成的缺陷在形状、尺寸和分布方面存在差异[25-28]。ALIYU等[26]研究了增材制造多孔钽诱导缺陷的形成机理,包括凝固诱导微孔、孔隙诱导微裂纹和凝固诱导微裂纹,以及后处理过程中多孔钽表面未完全熔化的钽粉颗粒脱落导致了微凹坑和微沟槽缺陷产生。区别于其他技术,微凹坑和微沟槽缺陷对目前直接应用于人体的多孔钽植入物力学和生物学性能有不利影响,体现为多孔钽丝杆局部边缘位置缺失,在载荷作用下更容易发生失效。3)在多孔钽植入物颗粒残留方面,由于钽粉熔融不彻底,多孔钽丝杆表面存在钽粉粉末附着的情况,目前缺乏增材制造多孔钽清洗工艺的研究,若钽粉颗粒去除不彻底,多孔钽产品在植入人体后,存在颗粒脱落的可能,从而引发并发症的风险会大幅提升,也同样对产品的安全性和有效性产生影响[29]。
本文作者综述了增材制造多孔钽的原材料、制备技术、力学研究、体内外评价和临床应用的相关进展,并结合团队多年来在定制式增材制造钽金属植入物的研究工作提出了增材制造多孔钽的未来展望。
1增材制造多孔钽的原材料
目前,主流的多孔钽增材制造工艺为粉末床熔融,其原材料为15~150μm粒径范围的医用球形钽粉。随着增材制造装备的成熟以及个性化多孔钽植入物需求的增加,从2015年开始,各国科研机构及粉末制造企业先后进行了球形钽粉工艺的开发[30],在钽粉球形度、流动性、松装密度、振实密度高和空心粉率等方面得到了很好的控制,目前其主要制备技术为等离子球化(PS)和等离子旋转电极雾化(PREP)(见图2[30-31])。钽粉的初始状态和粉末循环使用过程中性能的变化对多孔钽质量具有直接影响。在医疗器械认证过程中,钽粉及其回收再利用的质量控制措施是需要考量的技术要素之一[32]。目前,YY/T1851—2022和GB/T38975—2020是常用于评价粉末床熔融工艺用钽粉的可接受标准[33-34]。
PS技术原理为高温等离子体熔化载气输送的不规则钽粉的表面/整体,而后其在表面张力作用下缩聚成球形液滴,在冷却室中凝固成粉[31]。PS技术使用的原材料为钽粉,且设备投资大、运行费用高,因此,制备球形钽粉的整体成本较高。虽然PS技术球化效果好,但球化效率低以及在球化过程中容易发生氧污染,QIN等[35]报道了PS技术制备球形钽粉存在少量不规则、粗糙表面颗粒,在制备过程中使用了氩气保护,但氧污染仍然发生,能谱分析表明钽粉颗粒表面存在氧化膜,而颗粒内部氧含量较低。进一步地,HAO等[36]研究了不同工艺的原材料,以及载气流量、送粉速率和二次球化等工艺参数对球化钽粉的影响,结果表明,加氢脱氢钽粉比钠还原钽粉更适合于PS技术。球形钽粉质量的好坏最终体现在增材制造钽成形件的质量上,钽粉的氧含量是影响增材制造钽成形件微观结构和力学性能的重要因素。SUNGAIL等[37]制备了高氧含量和低氧含量钽粉成形件并进行了微观结构观察和力学性能测试,结果表明,低氧含量钽粉(87×10-6)成形件氧含量低(107×10-6),具有较高的伸长率和抗拉强度(35%,634MPa),拉伸断裂模式为韧性断裂。SHI等[38]采用481×10-6钽粉制备的成形件最大抗拉强度达到697MPa,伸长率为28.5%。LI等[39]对比了流态化、气流粉碎(JM)和PS技术制备钽粉的成形件性能,发现由于JM和PS技术制备的钽粉氧含量低,其成形件表现出良好的精度和较低的硬度。TAN等[40]研究了钽粉氧含量对增材制造工艺、微观结构和力学性能的影响,结果表明,低氧含量钽粉的工艺窗口更大,随着氧含量的增加(150×10-6→470×10-6),成形件晶粒结构从{100}||BD变为{111}||BD,极限拉伸强度增加(391 MP(42%→29%)。 SUNGAIL 和TAN 对成形件伸长率的研究结论存在差异,这可能受钽粉氧含量研究区间(SUNGAIL:87 × 10-6~829 ×10-6,TAN:150 × 10-6~470 × 10-6) 、成形设备和工艺等因素的影响。
图2 医用增材制造用球形钽粉的主要制备技术及难点[30-31]
PREP 技术原理为高温等离子体熔化高速旋转的自耗电极钽棒端面,熔融液膜在离心力作用下破碎成微液滴并凝固成粉[31],与PS 技术相比,PREP 技术是以高纯钽棒为原料,在生产成本、粉末形貌和杂质含量的控制方面优势明显[30]。然而PREP 技术制备的45 μm 以下球形钽粉收得率较低,一般小于10%。因此,提高PREP 钽粉的细粉收得率是该技术在多孔钽增材制造领域面临的主要挑战。
除了以往关注的增材制造工艺参数,最近的研究表明钽粉间隙杂质元素含量等因素对多孔钽的生物学性能、增材制造工艺稳定性和后续植入物质量 具有重要影响。一方面,氧等间隙杂质元素对BCC 结构钽具有很强的固溶强化作用,对钽的强韧性有显著影响[41],少量间隙氧原子有利于提高钽的强韧性[42]。另一方面,氧含量的增加降低了熔体的润湿和扩散能力,并阻碍了熔池的连接,导致部分熔池不稳定[40]。低氧钽粉(150×10-6)成形件的致密度对激光能量密度不敏感,而高氧钽粉(470×10-6)成形件在优化后的工艺参数条件下孔隙缺陷仍然增多、尺寸变大[40],说明氧含量的增加导致工艺窗口变窄。随着钽粉初始氧含量提高,样品中观察到沿晶断裂,断裂位置氧含量约为510×10-6,由于晶界处的氧元素富集[41],主要断裂模式由典型的韧性断裂转变为脆性和韧性断裂的组合断裂模式[37]。钽粉杂质元素氧主要来源于粉末中包裹的气体[41]。根据上述国内外的研究[31, 37-38],随着原料钽粉中氧含量的上升,增材制造钽的氧增量总体呈上升趋势,主要由于以下两个原因:1) 原料钽粉中氧含量(氧化物)的增加导致所需熔化能量更高,高能量密度作用下熔池停留时间长,导致凝固速度较慢,表面氧扩散到钽成形件内部的时间变长。2) 马兰戈尼对流更明显,导致飞溅钽粉颗粒与成形室氛围中氧杂质的接触面积增大。LEI等[43]的研究表明,由于低氧钽水接触角低,体内外试验表现出更好的成骨能力。因此,氧含量过高的钽粉不利于增材制造多孔钽的制备工艺和临床应用(见图3[35,40,42])。
钽粉价格相对较贵,在增材制造过程中循环使用可降低成本。金属粉末循环使用是以金属粉末为原料的增材制造技术特有的工艺状态,循环使用可极大提高粉末利用率。增材制造成形环境氛围,多次使用过程中的粉末回收、筛分、干燥、混合、存放等环节均有可能引入杂质元素,对粉末质量造成一定影响。《增材制造金属植入物理化性能均一性研究指导原则》(2022年第4号)提到,需验证回收粉末对打印过程和产品质量均一性影响。为了验证钽粉的可回收次数,作者团队系统地研究了增材制造钽粉循环过程中的粉末性能变化及其对钽成形件质量的影响[44]。在粉末性能方面,随着钽粉回收次数增加,钽粉氧含量逐步增加,从最初的46×10-6增至循环使用30炉的180×10-6。由于在真空环境下成形,单炉次钽粉氧增量平均仅为4.7×10-6,成形过程中飞溅、黏附及重熔导致钽粉的粒径略有增加,且由于粉末颗粒在循环使用过程中的烧结连接、破碎回收,粉末颗粒表面形貌变得不完整,因此流动性略有下降,但松装密度及振实密度均未发生明显变化。在成形件性能方面,同一工艺参数条件下有以下结论:1)实体钽的研究表明,钽粉重复使用过程中没有杂质引入,致密度呈下降趋势,拉伸强度无明显变化,而伸长率随着重复使用次数的增加而下降,再利用30次后的伸长率下降34.7%。2)多孔钽的研究表明,钽粉重复使用30次后,多孔钽孔隙率保持稳定,但表面球化现象增加(见图4[44]),压缩屈服强度和平台应力均下降约20%。综合上述研究,在多孔钽的增材制造过程中关注原材料钽粉的氧含量尤为关键。
图3 钽粉的氧含量影响增材制造多孔钽的生物相容性、工艺窗口和机械性能[35,40, 42]
图4 再利用30 次对钽粉和增材制造多孔钽表面形貌的影响[44]
2 多孔钽的增材制造技术
在临床治疗中,通过医工交互,可利用增材制造技术精确定制具有患者特定解剖特征的骨科植入物,同时可定制植入物不同区域的孔结构参数以满足人体骨组织对弹性模量的需求,避免应力屏蔽现象。增材制造是以三维模型数据为基础,通过材料堆积的方式制造零件或实物的工艺。根据技术原理,GB/T35021—2018和ISO/ASTM52900:2023将目前增材制造技术分为七类[45-46]。其中,选区激光/电子束熔化技术(SLM/EBM)由于具有精度高、效率高、稳定性好等优点,是增材制造金属骨科植入物中应用最广泛的技术,属于分类中的粉末床熔融工艺(PBF)。
2.1 SLM技术
利用SLM技术制备多孔钽植入物的工艺流程和技术原理如图5[13,44,47]所示,增材设备中具有合适参数的高能激光束选择性地熔化基板上铺设的钽粉,根据多孔结构模型数据逐层制造具有可控孔道的多孔钽成形件,整个成形过程在保护气氛下进行以避免氧化,使用切割机将成形件从基板上切割下来,通过喷砂等工序去除多孔钽成形件内部未熔化粉末,随后成形件经退火处理以消除加工过程中产生的残余应力,并通过清洗和灭菌包装获得最终多孔钽植入物。在制备过程中,多孔结构模型数据通过工程师进行植入物设计和模型打印前处理获得,适用于SLM技术的原材料钽粉粒度范围一般为15-53μm。
在SLM成形钽金属过程中,复杂的热过程导致不同形态钽成形件的微观结构存在差异[22,48-53]:1)不同工艺参数下的热输入引起的定向熔化和快速凝固。2)扫描策略。3)前一沉积层部分重熔。4)基板材质导热系数的差异,以及基板导致的特定热流方向等等。SLM成形块状致密钽的微观结构通常沿成形方向呈强烈的柱状晶粒,平均晶粒度约为54.7μm,大于传统锻造钽的平均晶粒度(约18.9μm)(见图6(a)和(c)[54]),SLM多孔钽的晶粒形状接近SLM块状致密钽,由于多孔钽的丝径通常在几百微米,热量更容易扩散至粉末,晶粒大小更接近于锻造钽(见图6(b)[55])。
图5 SLM 和EBM 技术制备多孔钽植入物的工艺流程和技术原理[13, 44, 47]
图6 钽的微观结构图[54-55]
增材制造多孔钽独特的微观结构和表面微纳米结构特征引起润湿性、表面能和生物性能等方面的改变更有利于临床应用。CHEN等[54]报道了与传统锻造钽对照组相比,SLM钽样品的大鼠骨髓基质细胞的黏附和增殖有所增强,其原因可能与SLM钽样品较高的表面能(64.42mN/m)和较低的接触角(Distilledwater40.03°)相关。根据VITOS等[56]的研究,钽的表面能从(110)、(100)、(211)、(310)到(111)呈上升趋势。CHEN等[54]的研究中,锻造钽以(110)为主,SLM钽在(110)、(211)和(310)方向分布。YANG等[57]通过SLM技术制备了小梁钽支架,并与美国捷迈公司的CVD小梁钽支架进行了比对,结果表明两者的多孔结构和力学性能相似,因此增材制造多孔钽存在骨填充和重建方面的应用前景,SEM观察进一步表明两者的丝杆表面均具有微纳米结构的表面,但前者的丝径和孔径更大,因此在制备生物医用精细多孔结构植入物方面,增材制造装备和工艺可进一步优化。
2.2 EBM技术
EBM技术制备多孔钽植入物的工艺流程和技术原理与SLM技术类似,不同之处在于:1)所采用的热源为电子束,成形过程在真空下进行。2)常用于EBM的原材料钽粉粒度范围一般为45~105μm或45~150μm。3)成形过程包含预热、热补偿工艺,因此,通常多孔钽成形件支撑简单且可直接拆卸,无需后续线切割、热处理等工序,有利于快速响应个性化植入物需求。
由于成形过程增加的基板预热、粉末预烧结和层间热补偿工艺,与SLM技术相比,EBM成形块状致密钽的微观结构沿成形方向的柱状晶粒更强烈(见图7(a)[53]),平均晶粒度增大(约89.5μm)(见图7(b)[42]),塑性优异,伸长率达到46%±12%[52],目前缺乏EBM成形多孔钽微观结构相关研究。
2.3 其他技术
基于成本降低或更好的生物学性能多孔钽的需求,研究人员尝试在其他增材制造方法上获得突破。激光定向能量沉积(DED-L)通过利用高能激光束将钽粉同步熔化沉积获得多孔钽,BALLA等[6]制备了孔隙率分别为27%和55%的多孔钽,并与多孔钛进行对照,验证了多孔钽具有更好的细胞黏附、生长和分化。CHEN等[58-59]制备了孔隙率在35.48%~50%的多孔钽样品,由于目前该工艺所采用的激光束光斑直径过大等因素导致了多孔钽的制造精度较低,限制了其在小孔径高孔隙率多孔钽中的应用。与粉末床相比,DED-L技术的钽粉原料通过载气输送,因此设备所需储粉量低且钽粉不易在多孔内部堆积,在节省成本和减少残余粉末风险方面具有很大优势。
图7 EBM 技术成形块状致密钽的特征[42, 53]
增材制造结合其他技术的混合制造方法有利于低成本、高性能、多功能的多孔钽植入物发展。WANG等[60]使用CVD工艺在SLM多孔钛合金支架上沉积了钽涂层,并通过体外和体内研究验证了钽涂层可以改善增材制造多孔钛合金的生物学性能。FOX等[61]采用SLM技术在钴铬合金表面成形了多孔钽涂层,通过微观结构表征两种金属材料之间的界面没有裂纹。通过在一个不同金属材料的底板上沉积多孔钽制备植入物,类似目前随形冷却模具中的嫁接增材制造方案,底座通常采用传统的机械加工完成,从而实现降本增效。ZHAO等[62]开发了一种基于增材制造凝胶灌制Ta2O5前驱体,然后采用电解还原法制备钽金属支架的混合方法,结果表明,制备的钽支架无毒且促进体外细胞黏附和增殖。通过凝胶灌制形成一级大孔,为新骨的形成和生长提供了受控的互联孔隙通道,然后采用电解还原法制备二级微孔,目的是促进细胞黏附、增殖和迁移,XRD结果显示Ta2O5还原成纯钽,但抗压强度低于5MPa。该方法利用廉价的氧化钽粉作为初始原料,成本较低,但仍需进一步优化多孔钽支架的力学性能才能满足临床需求。
3 增材制造多孔钽的力学和生物学研究
3.1 力学性能
生物医用多孔材料的力学性能显著影响新骨长入、骨整合和骨缺损物理功能替代[57],多孔钽应具备足够的屈服强度和较低的弹性模量,以适应骨组织的力学响应,减少应力屏蔽[63]。在骨科应用中,特别是承重骨假体领域,静态压缩性能是评价多孔材料的重要力学性能,表1[15,23,44,53-54,57,63-69]总结了粉末床增材制造多孔钽孔结构压缩性能研究。在过去的几十年里,已经建立了许多模型来联系多孔结构和力学性能,连接方式和孔隙率等因素影响着理论模型的适用范围[70]。Gibson-Ashby模型是一个常用于设计和预测多孔结构力学性能的经典模型,弹性模量(E和Es)、强度(σ和σs)与相对密度(ρ/ρs)之间的关系如下[71]:
E/Es = C1 ( ρ/ρ s )n (1)
σ/σs = C2 ( ρ/ρ s )n′ (2)
式中:下标s表示全致密材料;C1和C2为与单元支柱材料相关的常数;n和n’为指数因子。
由于增材制造多孔金属材料存在表面未完全熔化粉末、表面阶梯效应和内部缺陷等,一定程度上会影响模型预测力学性能的准确性。有研究发现,弹性模量受孔结构丝杆的影响比孔隙率更大[72],实际强度通常会低于理想状态下的强度[69]。结合上述章节对原材料和增材制造工艺的考虑,多孔钽的力学性能可能受以下方面影响[73-79]:1)钽本身力学性能,包括弹性模量、屈服强度和极限强度等。2)多孔钽孔结构的设计,包括孔单元形态、单元取向和单元组合排列方式等。3)可制造性,包括缺陷和晶格特征的保真度等。4)增材制造成形方向、摆放方向和制备炉/批次等。5)热处理、表面处理等。总体来说,多孔钽较低的模量意味着高孔隙率和合适丝杆形态,并且一般会伴随强度下降。对于多孔钽植入物,由于钽的高密度(16.6g/cm3),高孔隙率也有利于减轻重量和提高患者舒适度。
在SLM多孔钽的力学研究中,YANG等[23,47,65-66]研究了立方体(Cubic)、菱形十二面体(Dode)和仿生骨小梁(Trabecular)三种孔结构及其孔隙率对多孔钽的静态压缩行为的影响(见图8[23,65-66]):1)三种孔结构多孔钽的压缩强度随孔隙率的下降而提高。2)三种孔结构多孔钽材料失效机理为丝杆塑性变形与断裂,因此,这三种多孔结构多孔钽的力学可靠性优于多孔钛合金,立方体屈服点对应应变最大,抵抗变形能力最强,仿生骨小梁次之,菱形十二面体最低。3)立方体最大应力主要分布在纵向丝杆,仿生骨小梁和菱形十二面体主要分布在丝杆交接处,即失效位置。同时,他们研究了均匀结构、y梯度结构、z梯度结构多孔钽的动态压缩行为,y梯度结构由于断裂面上的局部体积分数最大,在三种不同梯度结构中表现出最好的平台应力和压缩模量,在不同应力的疲劳响应中,y梯度也优于其他两种结构。
在多孔钽结构创新方面,通过晶胞拓扑精细控制多孔结构力学性能对于长寿命个性化多孔钽植入物的设计至关重要。LI等[80]采用SLM技术制备了两种多孔钽支架(BCC和拓扑BCC-D)。其中,BCC-D的力学性能是各向异性,而BCC多孔钽在成形方向和水平方向的力学性能几乎相同,弹性模量和屈服强度分别接近1.9GPa和56MPa。如图9[63]所示,ZHANG等[63]基于SLM技术和马鞍的灵感,创新设计并制备了在不损失强度的情况下降低弹性模量的ISS结构,采用实验和有限元分析相结合的方法探讨了新型ISS结构多孔钽力学性能、变形机制和吸能特性,认为ISS晶格在承重骨科植入具有应用前景。
图8 Trabecular 结构多孔钛合金和多孔钽的压缩性能对比及三种孔结构失效点的图片[23, 65-66]
图9 ISS 结构设计在不损失强度的情况下降低弹性模量的示意图[63]
在EBM多孔钽的力学研究中,作者团队[67-69,81]研究了多种结构及其孔隙率对动静态压缩和静态拉伸、弯曲性能的影响。在压缩试验中,G7和立方体多孔钽以丝杆的屈曲变形为主,而菱形十二面体由于垂直支柱的存在,G7和立方体多孔钽的压缩疲劳强度和疲劳比均高于菱形十二面体多孔钽,立方体多孔钽的疲劳比最高,当菱形十二面体多孔钽丝杆角度从35.3°增加到43°时,通过增加屈曲变形,菱形十二面体多孔钽的疲劳强度和疲劳比分别提高了59%和20%。此外,在拉伸试验和弯曲试验中,菱形十二面体多孔钽最大应力分布均匀,均匀的结构变形延缓了丝杆的断裂,而G7和立方体多孔钽由于应力集中在部分位置上,使得变形初期就出现了丝杆断裂。根据不同孔隙率多孔钽样品的压缩、拉伸和弯曲性能测试结果绘图(见图10[69]),得出多孔钽力学性能与相对密度的关系如下:
E = 9.6(ρ/ρ s )2.05 (3)
σ 1 = 546.98(ρ/ρ s )2.9 (4)
σ2 = 613.93(ρ/ρ s )2.39 (5)
σ3 = 3262.11(ρ/ρ s )4.51 (6)
式中:σ1、σ2和σ3分别表示压缩屈服强度、弯曲屈服强度和拉伸屈服强度,与相对密度呈线性关系,指数因子n′分别为2.9、2.39和4.51,弹性模量和相对密度与指数因子n 为2.05,与Gibson-Assby 模型较一致。
图 10 多孔钽支架的力学性能与相对密度关系图[69]
图 11 疲劳试验期间梯度钽支架的宏观观察图:(a)VG; (b) PG[67]
此外,GUO等[67]研究了垂直梯度(VG)和平行梯度(PG)多孔钽的压缩疲劳行为和抗压疲劳强度。在疲劳试验中,PG多孔钽的失效集中在强度最低的成分上,导致了较高的棘轮应变和疲劳损伤应变(见图11[67])。在VG多孔钽中,由于各结构同时均匀变形,单个周期内的应变积累较小,导致循环棘轮应变较低。应力再分配会延缓高强度孔隙结构中疲劳裂纹的传播,从而降低疲劳损伤应变。因此,在相同应变条件下进行分级孔隙结构的设计思路,有利于获得具有高抗压疲劳强度的多孔钽支架,为高性能多孔钽植入物的设计和制备提供新思路。
3.2 生物学性能
多孔钽的孔结构参数是影响其植入物的力学和生物学性能的重要因素,包括孔单元形态、孔径、丝径、孔隙率、内部连通性等。一般认为,孔隙率和孔径与力学性能(包括弹性模量、强度等)、渗透性和生物性能(包括细胞黏附、增殖、分化、骨向内生长和骨整合等)高度相关,较高的孔隙率具有较低的弹性模量,可促进营养物质的运输和骨向内生长,但同时削弱了多孔钽的力学支撑[82]。
由于制备工艺、孔结构设计和测量方法等差异,目前多孔钽的体内外研究尚未得出最优的孔径和孔隙率参数组合。认可度较高的结论是平均孔径需要大于300μm才能支持血管化[83],目前临床上应用最成功的多孔植入物是美国捷迈公司骨小梁结构多孔钽,其孔隙率75%~85%,平均孔径400-600μm[4]。因此,对于新兴增材制造以及这项技术带来的工艺特征及孔结构设计自由度,研究不同孔结构参数组合以找到用于骨科的最佳增材制造多孔钽支架至关重要。表2[15,54,64,82,84-86]总结了粉末床增材制造多孔钽孔结构体内外实验研究,为增材制造多孔钽骨科植入物的进一步应用提供了新的依据。
4 增材制造多孔钽的临床应用
在过去二十多年中,多孔钽植入物冠以骨小梁金属TM(美国捷迈公司的TrabecularMetalTM)广泛应用于人体髋关节、膝关节及脊柱等全身部位。多孔钽的特性类似松质骨,与骨组织匹配的弹性模量、足够的机械支撑、较长的疲劳寿命、优异的耐腐蚀性和骨整合性能力保证了其在骨科和牙科等领域的应用前景。随着增材制造技术的发展,增材制造多孔钽凭借个性化优势已在多个部位实现临床应用,表3[53,87-91]总结了增材制造多孔钽在髋、膝等部位的临床应用。
1) Values in parentheses are design values, and values outside parentheses are measured values.
5 展望
在监管科学和共性技术研究方面,设计生产个性化多孔钽植入物时需获取、传递、使用和存贮数据,生物医用增材制造多孔钽基于合规、安全、可溯源和标准化等考虑应受到科学的监管。目前尚未建立生物医用增材制造多孔钽材料的评价体系,未能识别钽粉、多孔钽植入物的关键性能,测试项目多、质控成本高。关键参数/性能的低成本、快速、现场检测技术有待研发,从而方便追溯和提高质控水平。图12[92]所示为2023年Exum公司开发的用于固体材料快速化学表征的质谱仪,其能够对整个元素周期表进行痕量水平检测。美国LIFT称该检测设备有利于未来从粉末检测到组件设计、制造和测试新材料方面的工作,因为传统的实验室环境通常效率低下、元素检测范围有限以及通常需要外部检测[92]。增材制造多孔钽共性研究较少,加之钽价格昂贵,进一步提高了多孔钽植入物设计开发及商业化应用门槛,随着指导原则、标准的建立和检测技术的发展,增材制造多孔钽将得到进一步推广应用。
在多孔钽产品设计方面,拓扑优化和模拟仿真技术[93]的发展有利于设计和制造临床所需力学和生物学性能的多孔钽植入物。此外,将增材制造工艺特征约束到设计中,可使多孔钽植入物的设计兼顾可制造性,更好地实现所需仿骨多孔结构。
图 12 第一台激光烧蚀激光电离飞行时间质谱仪 Massbox 图片[92]
在多孔钽增材制造装备和工艺优化方面,目前个性化增材制造多孔钽的研究主要从临床角度进行评价,复杂个性化多孔钽植入物对制造、检测等影响有待进一步研究,如多孔结构形貌特征的保真度、多孔-致密复合钽植入物的连接界面金属粉末残留风险等。增材制造过程中对微观结构的控制是多孔钽实现生物医用功能的关键,因此,基于人工智能或机器学习的工艺参数优化、原位监测与缺陷预测的设备功能需求迫切,未来增材制造装备和钽粉规格根据多孔结构的极限特征和制造精度等差别,可能会更加专用化。
在增材制造多孔钽的服役评价方面,目前增材制造多孔钽植入物缺乏长期的临床结果,临床疗效也有待进一步论证。模拟真实服役条件,评估多孔钽植入物的疲劳寿命和失效模式,建立性能测试条件标准,才能真正反映是否达到所需性能要求和指导未来创新设计。
为提高多孔钽植入物的生物学性能,有必要探索新型表面改性技术,如通过抗菌涂层、仿生磷酸钙涂层、微弧氧化和表面功能改性等技术进一步提高多孔钽的抗菌性和成骨性能。此外,通过微观结构优化、增材制造多孔钛合金等高性能金属材料支架表面镀钽和多材料增材制造等技术,有望进一步提高增材制造多孔钽植入物的力学性能,满足承重需求。图13初步探索了增材制造多孔钽植入物设计开发过程和未来的研究方向。
6 结语
传统CVD工艺制备的多孔钽植入物已在临床上广泛地应用了二十余年,表现出优异的耐腐蚀性、生物相容性和骨整合能力,证明了多孔钽的安全性和有效性。增材制造多孔钽的研究已从工艺参数开发深入到缺陷机制和强化机理,通过力学性能和体内外生物学多方面评价不断优化多孔钽孔结构设计,并凭借个性化优势已在多个部位实现临床应用。此外,一些新的多孔钽增材制造工艺正在开发,包括增材制造多孔钛合金支架表面镀钽、钛钽多材料增材制造和增材制造新型多孔钛钽合金等等。随着增材制造技术的蓬勃发展,未来多孔钽的临床应用有望继续扩大。
图 13 增材制造多孔钽设计开发过程和未来的研究方向
参考文献:中国有色金属学报 林惠娴,等:生物医用增材制造多孔钽的研究进展
星尘科技使用射频等离子体球化技术生产的球形钽粉凭借优异的生物相容性与骨长入特性,广泛应用于脊柱、关节、创伤等临床医疗植入物的3D打印。星尘科技在国内率先实现医用级球形钽粉的产业化突破,与国内一流骨科医院、医疗器械公司等共同推进钽金属的临床医疗应用,先后参与制定GB/T 38975-2020增材制造用钽及钽合金粉、GB/T 41883-2022粉末床熔融增材制造钽及钽合金相关国家标准2项、YY/T 1851-2022用于增材制造的医用纯钽粉末行业标准1项、T/CAMDI 065-2021增材制造钽金属膝关节假体、T/CAMDI 066-2021增材制造钽金属个体化骨缺损填充体等团体标准3项,协助完成钽金属临床应用500多例,植入假体包括钽金属椎间融合器、骨垫块、髋关节、肩关节、膝关节、踝关节等。
咨询热线:13318326187 郑经理(微信同步)