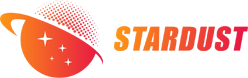
难熔金属钨及其合金具有熔点高、硬度大、高温强度高、弹性模量高、热膨胀系数低、导电性和抗腐蚀性能良好等优异性能,广泛应用于航空航天、国防军工、核工业、医疗装备、电子等尖端领域[1]。粉末冶金法是制备钨及钨合金最常用的方法。然而,由于钨及其合金常温下脆性较大,一些具有薄壁、曲面、多孔等复杂结构特征的零件很难通过常规粉末冶金法来制备,限制了钨及钨合金材料在工业领域的更广泛应用。
增材制造(additivemanufacturing,AM)是新一代“革命性”制造技术[2]。相较于传统的粉末冶金方法,AM具有材料利用率高、制造柔性高、加工余量小、结构设计约束少、可实现复杂结构零件的近净成形及对结构设计更改的快速响应等独特的技术优势,已成为当前钨及钨合金材料制备研究的热点之一。目前,激光选区熔化(selectivelasermelting,SLM)和电子束选区熔化(selectiveelectronbeammelting,SEBM)是制备钨及钨合金常用、研究较多的两种AM技术,国内外学者为此做了大量研究工作。本文简要介绍了SLM和SEBM技术的特点,详细综述了SLM和SEBM在制备钨及钨合金方面的研究现状,分析了存在的问题和不足,并对未来SLM和SEBM制备钨及钨合金成形件的发展方向进行了展望,以期为SLM和SEBM制备难熔金属成形件的后续研究提供一定参考。
1 SLM/SEBM技术
SLM制备金属成形件是利用激光对金属粉末依据设定路径快速熔化、逐层凝固堆积而实现成形件的制备技术[3-4],其原理如图1所示[5]。在制备过程中,采用惰性气体(高纯Ar或N2)进行保护,以防止金属在高温下与其他气体发生化学反应。激光/粉末的相互作用向粉末床输入很高的能量,使金属粉末床产生很大的温度梯度,产生传热、传质及相变等物理化学冶金过程。SLM技术用于制备形状复杂的零件,尤其是具有复杂内腔结构和具有个性化需求的零件,适合于多品种、小批量成形件的快速制备,具有广阔的发展前景。
Fig.1 Schematic diagram of SLM technology[5]
相比于SLM技术,SEBM以高能电子束为热源进行铺粉、预热、熔化循环逐层堆积实现成形件制备[6]。在制备过程中,腔室内保持较高真空度,适用于对氧、氮等敏感的活泼金属和合金的制备[7]。SEBM技术具有能量利用率高、成形效率高、成形应力低和成形过程真空洁净等特点,广泛应用于纯铁和钢、钛和钛合金、镍基高温合金、钴基合金、铜和铜合金、Co-Cr-Mo合金、TiAl以及难熔金属等材料的制备[8]。另外,SEBM的粉末预热功能可将成形件保持在较高温度(可达1000℃以上),对于降低零件内部的残余应力具有显著效果,是具有良好前景的钛铝基合金先进制造技术之一[9]。SEBM提高了成形件制备的质量和效率,降低了生产成本。但SEBM仍存在诸多问题,如制备的成形件表面质量差、尺寸精度差等,仍需要进一步研究[10]。SLM/SEBM特点对比如表1所示[3,6,10]。
表1 SLM/SEBM特点对比
2 SLM/SEBM制备钨及钨合金成形件的研究现状
近年来,从公开发表的研究论文数量变化情况来看,SLM和SEBM制备钨及钨合金成形件的研究呈现剧增趋势。许多国家和科研机构对此开展了大量研究工作,国外主要有美国、德国、英国、日本等国家,国内清华大学、南京航空航天大学、中南大学、华中科技大学、西北有色金属研究院等科研院所,主要围绕原料粉末、成形工艺和合金化等因素对钨及钨合金成形件的致密度、微观组织、力学性能和缺陷等方面的影响开展研究,大量工作主要集中在纯钨方面,而对W-Ta,W-Nb,W-Re,W-Y2O3,W-TiC,W-ZrC等钨合金[11]以及W-Ni-Fe等合金的研究较少(图2),其成形件制备技术主要集中在SLM上。
2.1 SLM制备钨及钨合金成形件的研究现状
在SLM制备钨及钨合金方面,原料粉末、成形工艺、合金化和后处理对成形件的显微组织、力学性能等影响非常大。
2.1.1 原料粉末方面原料粉末是影响SLM制备钨及钨合金成形件性能的重要因素,粉末形貌和粒度直接影响激光与粉末之间的相互作用。与不规则粉末相比,由于球形粉末堆积密度大,激光与粉末颗粒相互作用时,光束在颗粒之间多次反射吸收概率也大。研究表明,不规则粉末的激光吸收率为50%,而球形粉末的激光吸收率为68%[12]。Zhang等[13]基于线迹追踪模拟计算的结果表明:激光作用于粉末颗粒时,激光在粉末颗粒之间的多次反射加强了相邻粒子之间的相互作用,大大促进了激光的吸收;但随着粉末粒径增加,粉末层的激光吸收率下降;钨粉末层最大激光吸收率为0.6030(钨粉粒径为5μm)。
图 2 SLM/SEBM 技术制备钨及钨合金材料种类
国内外多位科研人员研究了原料粉末形貌对SLM制备纯钨成形件性能的影响[12,14-16]。Wang等[12]以常规粉末和球形粉末为原料为原料,分别获得致密度84%和96%的纯钨成形件,如图3所示。Zi等[14]也开展了此方面的研究工作,分别获得致密度为90.9%和96.9%的成形件,如图4所示。可以看出,以不规则粉末制备的成形件内部存在明显的孔洞和裂纹,而球形钨粉制备的纯钨成形件内部存在少量的裂纹和气孔。图5为以不规则粉末和球形粉末为原料进行SLM制备纯钨成形件的致密度。相比于常规钨粉,球形粉末具有较高的激光吸收率,有利于连续扫描轨迹的形成和成形件的致密化。Yamamoto等[15]以不规则钨粉为原料制备的纯钨成形件致密度达98.58%,而Rebesan等[16]以球形钨粉为原料制备的纯钨成形件致密度达99.61%。
为此,国内外许多科研机构,如美国亨茨维尔等离子工艺有限公司、加拿大Tekna等离子系统公司、北京科技大学和核工业西南物理研究院等,均开展了高质量球形钨粉制备研究工作,以满足SLM对粉末性能的要求。
图 3 原料钨粉及SLM制备纯钨成形件形貌(扫描电镜(SEM)图像)
图 4 SLM 制备纯钨成形件形貌(SEM 图像)
图 5 不同粉末形状条件下 SLM 制备纯钨成形件的致密度
2.1.2 成形工艺方面
调整成形工艺实现调控材料组织和性能是SLM制备成形件常用且重要手段,在一定程度上可以实现提高材料性能的目的。成形工艺主要包括:成形工艺参数、扫描策略、基板、腔室气体等方面。
(1)成形工艺参数方面
在SLM制备成形件过程中,多个工艺参数共同影响成形件最终性能。这些工艺参数主要包括:激光功率、扫描速度、铺粉层厚和扫描间距等。其中Enneti等[17]认为扫描速度是影响成形件致密度的主要因素。目前,国内外学者一般选用输入能量密度来衡量成形件制备过程的能量输入大小。输入能量密度主要分为线能量密度(line energy densi⁃ ty,EL,J·mm-1)[18-20]、面能量密度(areal energy den⁃ sity,ED,J·mm-2)[21-22]和体能量密度(volumetric en⁃ ergy density,EV,J·mm-3)[5,23-25]这3种,其计算公式分别为:EL=P/v,ED=P/(v·h)和 EV=P/(v·t·h)。 其中,P 为激光功率,W;v 为扫描速度,mm ·s-1;t 为铺粉层厚,μm;h 为扫描间距,μm。不过,大多科研人员常常采用 EV 来衡量输入能量大小。在不同能量密度条件下,SLM 制备纯钨成形件的相对密度如图6所示,其中纯钨成形件相对密度达90%以上的科研机构占85.7%。
在 SLM 制备成形件过程中,激光能量的输出方式有连续输出模式和间断脉冲模式。南京航空航天大学等[5,20,26,34-35]、清华大学等[12,22,28]科研院所分别以连续输出模式和脉冲输出模式激光作为能量输入源,研究了 SLM 工艺参数对纯钨成形件性能的影响。在实验研究开展方面,单道是最基本的成形单元,最终成形件本质是单道堆积而成,单道 的成形质量直接影响最终成形件的质量。因此,科研人员一般先采用单道扫描研究各个工艺参数对熔池轨迹形貌、几何特征、缺陷等方面的影响,获取合适的成形工艺参数窗口,初步实现成形工艺参数的筛选和优化,再依据单道扫描的研究结果进行实体件制备。单道扫描轨迹是获取 SLM 制备成形件工艺参数窗口的有效途径。
图 6 不同输入能量条件下SLM制备纯钨成形件的相对密度
在激光以连续输出模式方面,Gu等以EL衡量输入能量大小,采用先单道扫描、后实体件制备的实验方法研究激光功率和扫描速度对成形件性能的影响,如图7所示[34]。在扫描轨迹表面特征方面,合适的EL可以获得无裂纹规则的扫描轨迹(图7(b,b1));而输入能量不足导致液态金属流动前沿不规则,使扫描轨迹出现明显收缩现象,也会存在未熔化和飞溅现象(图7(a,a1,g~i1));输入能量过高造成液态金属熔池存在较大的温度梯度和冷却速率,扫描轨迹表面会产生裂纹缺陷(图7(c~e1))。在扫描轨迹几何特征方面,激光功率增加和扫描速度降低使EL得到提高,造成扫描轨迹高度和接触角降低、熔池宽度和深度增加。在扫描轨迹熔池横截面形态演变方面,当 EL>1.5 J ·mm-1时,扫描轨迹熔池呈匙孔模式;当 EL≤1.5 J ·mm-1时,扫描轨迹熔池呈热传导模式。依据单道扫描研究结果,该团队获得相对密度为98.4%,内部无明显气孔和球化现象的纯钨实体件,显微硬度和抗压强度分别为HV474和902MPa,磨损率为1.3×10-5mm3·N-1·m-1[5]。
另外,牛朋达等[26]和Zhang等[35]采用SLM制备了晶粒细小的纯钨成形件。牛朋达等[26]制备了晶粒小于1μm的等轴晶成形件(图9),显微硬度为HV485,远远高于粉末烧结样品的显微硬度。Zhang等[35]制备了晶粒尺寸约为500nm的纯钨成形件,在较大激光能量输入条件下,细小晶粒由相互缠结生长转为相互垂直生长(图10)。
Wang等[12]、Huang等[22]和Sidambe等[28]以脉冲输出模式激光作为能量输入源开展研究工作,脉冲模式下的影响因素主要有激光功率、曝光时间、点距和扫描间距等。Wang等[12]研究激光功率和曝光时间对纯钨成形件表面形貌的影响(图11)。结果发现,在不同的激光功率和曝光时间条件下,出现致密区域、连续区域和球化区域。在点距为70μm时,成形件获得相对密度高达96.0%,硬度为3.79GPa。输入能量密度较小或过大均易产生球化现象。作者认为点距和扫描间距是影响成形件性能的因素,二者的选择必须确保相邻扫描轨迹的重叠。
图 7 不同输入能量条件下 SLM 制备纯钨成形件的扫描轨迹表面形貌(SEM 图像)
Huang等[22]在研究扫描间距和点距对成形件气孔的影响方面开展了工作,制备了相对密度为92.5%的纯钨成形件。表观孔隙是扫描间距和点距较大条件下成形件内部产生的未熔合缺陷,其随着扫描间距和点距的增加而增加。而闭合孔隙是由于较小的扫描间距和点距造成的飞溅和匙孔,其随着扫描间距和点距的增加而减少。块体内孔隙主要以表观孔隙为主。Sidambe等[28]认为激光能量密度足够用于制备纯钨成形件,其致密度可达98%,可以满足W准直器和其他面向等离子体材料的性能要求。
图 8 不同输入能量条件下 SLM 制备纯钨成形件性能
图 9 SLM 制备纯钨的显微组织(SEM 图像)
图 10 不同扫描速度条件下SLM 制备纯钨的显微组织(SEM 图像)
图 11 不同工艺参数下SLM 制备的纯钨成形件表面形貌(SEM 图像)
此外,SLM在制备高附加值、小批量和复杂结构难熔金属成形件方面具有巨大优势。Deprez等[37]采用SLM制备了致密度为89.92%±0.5%的纯钨准直器成形件(图12),尺寸精度为-260~650μm,孔径位置平均偏离5μm,平均孔径尺寸为(464±19)μm,计算和测量的点源在视场中不同位置的灵敏度和分辨率符合较好。Xie等[38]也制备了纯钨格栅件,激光功率对薄壁件的壁厚影响较大,过高的激光功率会产生热裂纹,优化工艺参数可以降低薄壁件表面粉末粘附问题。
(2)扫描策略方面
扫描策略是SLM制备钨及钨合金成形件的又一重要因素[39-40]。较高的能量输入和温度分布不均匀会使熔池内部温度梯度大,造成成形件内部存在较大的残余应力,甚至导致成形件翘曲变形。常用的扫描策略有:双向扫描、岛状扫描和重熔扫描,扫描矢量为无旋转、旋转67。和旋转90。(表2)。
图 12 纯钨准直器成形件
Gu等[41]研究了岛状扫描、重熔扫描和双向扫描策略对SLM制备纯钨成形件性能的影响(图13和表3)。结果表明,岛状扫描策略由于能量传递不连续,岛与岛之间的能量分布不均匀,较易于产生网状裂纹。同时,在层与层之间,凝固过程的不均匀收缩累积会导致成形件内部产生沿制备方向的长裂纹,如图13(a1~a5)所示。重熔扫描策略可以减少成形件内部气孔,降低残余应力,制备的成形件表面质量好、缺陷较少,但重熔策略会使成形件组织晶粒粗大,给成形件的力学性能带来不利影响,如图13(b1~b5)所示。双向扫描策略由于能量传递连续,即使液态金属凝固过程收缩不可避免,但在一定程度上减少了成形件的裂纹,如图13(c1~c5)所示。根据以上3种扫描策略的研究结果来看,旋转67。及双向扫描策略制备的成形件力学性能最高。
在研究重熔扫描策略影响SLM制备纯钨成形件性能方面,Xiong等[30]采用1/2EV输入能量的重熔扫描策略使纯钨成形件内部晶粒细化,这主要是由于重熔引起液态金属对流造成的,与Rebesan等[16]观点一致。Zhou等[29,51]认为重熔策略可以减弱SLM制备纯钨成形件的球化现象,使成形件致密度提高。不过,Xiong等[30]认为重熔过程可能会导致液态金属流动带入保护气体,使成形件的致密度降低。另外,重熔策略可以减小成形件内部的残余应力,但不能完全抑制裂纹的产生[30,41]。
表2 SLM 技术制备钨及合金成形件的扫描策略(BD:成形方向;TD:横向;SD:扫描方向)
图 13 不同扫描策略下 SLM 制备纯钨形貌和组织(SEM 图像)(激光功率:300 W,扫描速率:300 mm ·s-1,铺粉层厚:20 μm, 扫描间距:50 μm)
表3 不同扫描策略条件下SLM 制备钨成形件的对比
Wang等[24]研究了无旋转、旋转67。和旋转67。且重熔的双向扫描策略对SLM制备纯钨成形块体件裂纹和微观组织的影响(表4)。结果表明:旋转67。扫描策略可以使晶界相互缠绕,提高裂纹扩展阻力,有利于抑制裂纹扩展。Wen等[19]和Zhou等[29]认为相邻层间扫描矢量旋转67。可以减小成形件内部残余应力,制备的成形件晶粒细小,无明显织构产生。Braun等[18]的实验证明,相比于相邻层间旋转90。,相邻层间旋转67。是更佳的扫描策略。纯W具有高裂倾向性,SLM制备纯钨成形件,裂纹是不可避免的问题,采用相邻层旋转扫描可使成形件内部晶界相互缠绕,有助于抑制裂纹的扩展。
表4 不同扫描策略条件下SLM 制备钨成形块体件的对比
目前,相邻层扫描矢量旋转67。的双向扫描策略应用范围最广。
(3)基板方面
基板是影响SLM制备纯钨成形件性能的另一个因素。基板预热、表面处理和基板材质影响熔池的温度分布和温度梯度,对成形件内部的残余应力产生重要影响。
在基板预热方面,大多采用低温(低于200℃)预热基板。理论上讲,基板预热温度高于纯钨的韧脆转变温度(DBTT),螺位错具有足够高的迁移能力,可以满足熔化和冷却过程中因温度梯度引起的塑性应变。Ivekovic等[23]和Wang等[24]认为可以通过提高预热温度减少成形件内部的裂纹。Müller等[31]认为提高基板预热温度,可以提高成形件的致密度,最大可达98%(图14)。而Kaserer等将基板预热温度达到1000℃也不能避免SLM制备钨成形件中裂纹的产生[18]。
在基板表面处理方面,周鑫和刘伟[51]对基板进行黑漆处理,提高基板对激光的吸收率。研究表明:经黑漆处理表面的基板,增强了基板/粉层对激光的吸收,有助于提高熔滴峰值温度并延长凝固时间,因而可以减弱纯钨熔滴球化倾向。
基板材质会通过影响液态金属的凝固速率来影响成形件的性能。在基板材质方面,大多数研究者选用不锈钢(导热系数为10.0~34.3W·m-1·K-1)作为基板。Sidambe等[28]采用纯钛(导热系数为17.0W·m-1·K-1)作为基板制备纯钨(导热系数为163.3W·m-1·K-1)成形件,纯钛降低了熔池的冷却速率,使熔池在高温阶段保持较长时间,有利于成形件的制备成形。周鑫和刘伟[51]以及Li等[43]选用纯钨基板,后续加工过程可以不考虑基板引入的杂质问题[52-53]。
图 14 钨成形件相对密度(基板预热温度:600.800和1000℃; 激光功率:375和400W)
(4)腔室气体方面
大多数研究者选用氩气(Ar)作为腔室气体,少数研究者选用氮气(N2)。Dong等[32]研究了腔室气体对SLM制备纯钨成形件性能的影响。以Ar作为腔室气体,液态金属钨具有较高的粘度,易产生球化和气孔,导致制备的纯钨成形件相对密度较低,机械性能较差。与Ar相比,以N2作为腔室气体,W和N2形成了钨的氮化物,降低了液态金属的表面张力和粘度,制备的纯钨成形件表面质量得到提高。N2条件下的快速冷却还使其具有较高的硬度和强度。因此,N2条件下SLM制备的纯钨成形件具有更高的密度、较低表面粗糙度、更优良的力学性能(表5)[43],腔室气体选择N2更有利。Zi等[14]采用N2作为保护气体获得致密度达96.9%的纯钨成形件。此外,Yamamoto等[15]也认为纯钨成形件内部纳米孔是由于保护气体Ar的滞留而造成的,可以选择在真空条件下制备纯钨成形件,或者选用较小原子尺寸、较高扩散系数的N2作为保护气体。
2.1.3合金化方面由于纯钨的表面张力大、粘度大、润湿性差,导致制备的纯钨成形件存在球化、气孔、裂纹等缺陷,这是SLM制备纯钨成形件中最常见的3种缺陷。除了从前文原料粉末和成形工艺两个方面改进外,部分研究者还在纯钨中添加一定量的Ta,Nb,ZrC和Y2O3等组分,改善纯钨成形件性能。
(1)SLM制备纯钨成形件缺陷的产生
球化现象是SLM制备纯钨成形件的缺陷之一。Zhou等[29,51]以100μm的纯钨熔滴为研究对象,计算其在6000K(接近纯钨沸点)时液态金属纯钨完全铺展时间为86.3μs,而其凝固时间为46μs;在熔点附近时,液态金属纯钨凝固时间为7.6μs,这使得液态金属纯钨在凝固过程中易产生球化现象。SLM制备纯钨成形件的球化现象如图15所示[29]。除钨自身特点外,球化现象还与材料中的氧有关,氧会影响液态熔池表面张力和毛细对流,进一步加剧球化倾向。
表5 不同腔室气体条件下SLM制备纯钨成形件性能
图 15 SLM 制备纯W成形件上表面形貌(SEM图像,曝光时间200μs条件下)
裂纹是SLM制备纯钨成形件的主要缺陷之一,探究其开裂机制是目前研究的热点问题[54-55]。SLM制备纯钨成形件中的裂纹倾向于沿大角度晶界扩展,这主要是由于纯钨成形件内晶界对杂质的敏感性。Kaserer等认为杂质氧是造成纯钨成形件裂纹和气孔的主要原因[18]。在制备过程中,氧以钨的氧化物形式在晶界处偏析,削弱晶界结合强度,增加冷裂纹的风险,提高了纯钨的DBTT。快速冷却过程中,平面凝固晶界热裂纹和沿弱化晶界冷裂纹的结合形成了SLM制备纯钨成形件中普遍存在的裂纹网络。Vrancken等[36]认为微裂纹出现在450~650K之间的狭窄温度区间内,凝固和裂纹之间的时间延迟与P/v存在线性关系。
气孔是成形件中常见的另一种缺陷形式[19]。气孔的形成原因大多归因于工艺参数、原料粉末和腔室气体等方面。在工艺参数方面,能量输入不足、扫描间距较大会造成未熔合气孔的形成;能量输入过大会使液态金属蒸发,蒸汽在熔池冷却凝固过程来不及逸出,会在成形件内部产生圆形气孔。在粉末原料方面,粉末颗粒自身不致密是造成成形件内部气孔的原因之一。此外,在SLM制备纯钨成形件中,腔室气体易被卷入熔池而来不及逸出,也易产生气孔。成形件内的气孔影响其致密度和力学性能,可以通过优化工艺参数、选择合适扫描策略、合金化和后处理等措施来减少成形件内的气孔缺陷。
(2)合金化
为了消除和抑制SLM制备纯钨成形件的缺陷,清华大学[25,44]、西安交通大学[45]、西安空军工程大学[46]、比利时鲁汶大学[23]等研究机构采用在纯钨中添加一定量的Ta来抑制SLM制备纯钨成形件内部裂纹的产生。Wang等[25]认为钨的氧化物汽化形成的纳米孔,大多分布在纯钨成形件的晶界处,是导致裂纹萌生的主要原因。而W中添加6%Ta后,W-6%Ta合金晶粒内存在亚微米胞状结构,纳米孔大多聚集在晶粒内部的胞状结构处。故作者认为W-6%Ta合金没有抑制纳米孔的形成,而是改变其分布位置(图16)。不过,相比于纯钨成形件,W-6%Ta合金中裂纹减少80%,裂纹得到有效抑制。Li等[44]认为由于钽与氧的亲和力高于钨,添加钽可以吸附晶界处的氧,形成钽的氧化物纳米颗粒(Ta0.8O2,Ta0.83O2和TaO2)作为异质形核核心,从而降低晶界处氧含量、细化晶粒,提高成形件抗裂纹扩展阻力,使制备的W-6%Ta合金裂纹密度降低30.7%。Ivekovi等[23]认为Ta的加入提高了W的硬度和再结晶温度,降低了纯W的导热系数,也有利于纯钨成形件的制备。
此外,Yamamoto等[33]通过在W中添加一定量的铼,使成形件内部裂纹密度降低59%。Li等[43]通过在W中加入0.5%ZrC使晶粒细化,减少晶界处氧杂质浓度,提高晶界强度,裂纹密度降低88.7%。Hu等[47]通过在W中添加纳米级1%Y2O3,使成形件内大角度晶界明显减少,抑制纯钨成形件的裂纹生长和扩展,使成形件内部裂纹明显降低。Gu等[42]和Xue等[50]也分别发现通过添加一定量的纳米级TiC或Nb对改善和减少纯钨成形件内部的裂纹也有一定作用。
图 16 SLM 制备纯钨和 W-6%Ta 成形件内纳米孔分布的电子通道衬度成像(ECCI)图
2.1.4后处理方面合适的热处理可以消除成形件内部的残余应力,减少气孔,提高成形件性能。张梦晗等[21]对SLM制备的纯钨成形件进行1400℃热处理,使得成形件的抗弯强度和显微硬度得到提升。Ren等[27]的相关工作表明,纯钨成形件退火后最大抗拉强度为1.007GPa。Yamamoto等[15]认为纯钨成形件内部纳米孔是由于保护气体Ar的滞留而形成的,经1900℃×2h热处理后,纳米孔降低50%,成形件的力学性能和热导率得到了提高。而Guo等[46]采用原位退火工艺处理的W-12%Ta合金薄壁成形件,其硬度值达4.6GPa,弹性模量达179GPa。
此外,部分研究者对SLM制备的W-Ni[56],W-Ni-Fe[48-49],W-Ni-Cu[57]和W-Ni-Fe-Co[58]等合金也进行了研究。Zhang等[56]采用SLM制备了Ni含量为10%,20%和40%的W-Ni合金成形件,由于Ni引起的成分过冷,其显微组织分别为柱状晶、树枝晶和蜂窝结构的胞状晶。SLM制备的90W-7Ni-3Fe(%,质量分数)成形件,由于激光能量的输入不同,不同区域晶粒从胞状晶转变为树枝晶[48]。SLM制备的W-10Ni-10Cu(%,质量分数)成形件显微组织内存在非晶态W-Ni固溶体[59]。Li等[49]制备了相对密度≥99%的90W-7Ni-3Fe(%,质量分数)成形件,其最大抗拉强度(UTS)达1121MPa,延伸率<1%,平均硬度>HV0.3400。Iveković等[57]还对W-7Ni-3Fe(%,质量分数)成形件进行热处理,与Li等[49]所得结果相比,成形件的抗拉强度降低,而延伸率得到提高。Chen等[58]采用SLM制备W-Ni-Fe-Co成形件,认为激光参数对W-Ni-Fe-Co的延伸率没有明显影响。
2.2 SEBM制备钨及钨合金成形件的研究现状
近年来,SEBM因其自身优势也逐渐应用于复杂结构成形件的制备,材料种类方面有纯钨[60-65]和钨合金[66-69]等。目前,SEBM制备钨及钨合金成形件的研究院所国内有西北有色金属研究院、北京大学、东北大学等,国外如德国于利希研究中心、美国田纳西州橡树岭国家实验室等。SEBM制备成形件主要受熔化电流、扫描速度、铺粉层厚和扫描间距等因素的影响。
在纯钨成形件制备方面,Ren等[60]、Yang等[61-62]、杨鹏伟[63]以及Dorow-Gerspach等[64]采用SEBM制备了近致密的纯钨成形件,其显微组织为沿着制备方向的粗大柱状晶。不过,由于电子束的能量利用率高和钨的导热系数高,基板温度始终保持在800~950℃,有利于成形件内部残余应力的释放。Ren等[60]采用SEBM制备出相对密度为98.93%,内部无裂纹、仅有少量气孔的纯钨成形件,其柱状晶尺寸为320μm,晶粒取向为<100>,抗压强度达1.76GPa。Yang等[61-62]和杨鹏伟[63]制备了致密度为99.5%,内部仅存在微裂纹的纯钨成形件,柱状晶长约200μm,宽为50~150μm,<100>和<111>为柱状晶沿着成形方向的择优取向,成形件抗压强度达1560MPa,维氏硬度达HV500以上,高于传统工艺制备的纯钨成形件。Dorow-Gers⁃pach等[64]也采用SEBM制备了相对密度为99.5%,柱状晶宽度100~200μm的纯钨成形件,其硬度约为HV10350,接近再结晶纯钨的硬度。作者还认为在SEBM工艺中,仅仅考虑线能量密度对成形件的致密度和质量的影响不充分,还应考虑电子束功率的大小。同时实验结果也表明,SEBM制备的纯钨成形件在稳态和瞬态热载荷方面表现出与常规再结晶钨相似的性能。Ellis等[65]还将原位缺陷检测算法应用于纯钨内部孔隙率的检测来研究电子束粉末床熔合(EB-PBF)工艺参数对纯钨成形件缺陷密度的影响,作者认为较高的预热温度、较大的输入能量可以制备致密、无裂纹的纯钨成形件,并指出纯钨成形件内部的裂纹主要与氧含量有关。未来可以从能量密度对成形件表面形貌的影响机制和添加碳化物或氧化物使SEBM制备的纯钨成形件晶粒细化两个方面来进一步研究。
在钨合金方面,杨广宇等[66]采用SEBM制备了W-3.5%Nb合金,研究了高速扫描、低速扫描和两次扫描对成形件微观组织和熔合不良、微裂纹缺陷的影响。结果表明,熔合不良主要由熔池的球化和扰动导致,微裂纹主要是由凝固过程中枝晶间液相的凝固收缩引起。在高速扫描时,由于扫描层间熔合不充分,晶粒外延生长不明显,导致形成细小等轴晶,没有明显的择优取向,熔化层表面存在大量的缩孔,制备方向存在大量的熔合不良缺陷。低速扫描时,在外延生长的作用下,会形成粗大的柱状晶组织,并沿成形方向形成(001)择优取向,而缩孔和熔合不良缺陷明显减少。研究结果还发现,在单层两次熔化条件下,柱状晶特性和晶粒的择优取向减弱,但熔合不良缺陷未能完全消除,且相比于低速扫描时,熔合不良缺陷略有增多。全俊涛等[67]认为采用两种不同扫描路径先后对金属粉末层进行扫描,会使零件应力分布更均匀,不易导致其翘曲变形,也可以在一定程度上改善零件熔合不良的缺陷。
此外,Konyashin等[68]也采用SEBM获得致密的WC-13%Co成形件,其上表面粗糙度Ra=4.4μm,Rz=22.8μm(Ra是指在取样长度内轮廓偏距绝对值的算术平均值;Rz是指在取样长度内5个最大的轮廓峰高的平均值与5个最大的轮廓谷深的平均值之和),侧面粗糙度Ra=24.5μm,Rz=142.3μm,几乎与原始WC-Co颗粒的平均尺寸一致。制备出的含有2%气孔率的成形件经过热等静压(HIP)处理后,可消除中间区域的气孔。Xiao等[69]也采用SEBM技术制备了致密度达98.5%的WTaRe难熔金属高熵合金。
3 总结与展望
通过AM技术制备高性能、复杂结构的钨及钨合金成形件,为钨及钨合金开拓了更加广阔的应用领域。影响AM制备钨及钨合金成形件的主要因素有原料粉末、成形工艺(成形工艺参数、扫描策略、基板、腔室气体)、合金化和后处理等。目前,尽管众多研究者在此方面进行了大量研究,但仍存在一些问题需进一步研究,主要集中在以下几个方面:在材料体系方面,纯钨成形件的制备研究及缺陷机制研究较深入系统,而对钨合金方面研究较少;在制备工艺方面,大量研究工作围绕SLM开展,而SEBM相关研究不多;在材料性能方面,SLM成形件存在诸如内部裂纹尚未实现完全消除、SEBM成形件表面粗糙度大等问题;在数值模拟方面,目前尚未很好建立工艺参数-微观组织-缺陷特征-力学性能的内在联系,以快速实现成形工艺的调控和优化等。因此,如何克服和解决上述问题仍是未来钨及钨合金材料增材制造研究的重点和热点。
参考文献:增材制造制备钨及钨合金材料研究进展 - 百度学术 (baidu.com)
星尘科技采用先进的射频等离子体球化工艺制备球形钨粉和钨合金粉。这些粉体具备以下显著优势:
高纯低氧:通过精密的工艺控制,粉体中的杂质含量极低,保证材料的高纯度,适合高要求的工业应用。
球形度高:粉末颗粒呈现高度球形,有助于在增材制造过程中实现更均匀的沉积和更高的成品质量。
粒度可控:可以根据具体需求调节粉体的粒径范围,满足不同应用场景的要求。
流动性优异:球形颗粒结构和优化的粒度分布确保了粉体在增材制造设备中的顺畅流动,提高了生产效率。
这些特性使得星尘科技的球形钨粉及钨合金粉成为增材制造(如3D打印)等高端制造领域的理想选择。
更多稀有难熔金属球形粉末,请咨询我们专业的技术人员。郑经理13318326187