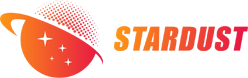
难熔金属是指熔点大于2000℃的金属材料,主要包括钨、钼、钽、铌、铼、钒等6种金属元素,还有以该6种金属元素为基础的合金材料[1]。由于具有高温性能好、抗蠕变能力强、熔点高等优异的综合性能而被应用于航空航天、装备制造、核工业等尖端领域[2-4]。传统的难熔金属制备方法主要包括烧结法和熔炼法,然而此类方法生产流程较长、原料利用率较低、成本较高,使难熔金属的应用和发展受到限制。近些年来,随着增材制造技术的快速发展,为解决难熔金属制备及加工问题提供了新的发展思路[5]。
增材制造是通过添加粉末材料层来制造具有复杂形状构件的制造技术。在国际标准ISO/ASTM52900中,增材制造的定义为将材料从3D模型数据连接成零件的过程[6]。在金属材料增材制造领域,一般采用激光和电子束等高密度能量热源进行选区熔化,按照不同的能量来源分类,目前最具代表性的为选择性激光熔化(selectivelasermelting,SLM)[7]技术和电子束选区熔化(electronbeamselectivemelting,EBSM)[8]技术。SLM技术是采用激光源输入能量,在选定区域中熔化金属粉末,该技术的主要工艺参数包括输入能量、扫描速度、填充空间和层厚,通过调整以上参数,可获得近全致密的金属构件。EBSM与SLM具有相同的工作流程,与SLM的主要区别在于EBSM采用电子束来代替激光束作为能量源,该技术以高速电子轰击和高功率密度著称。在制造过程中,为了避免电子束冲击粉末时产生飞溅,需要对粉床进行预热,预热过程中,在高电子束流和超快的扫描速率(≥103mm/s)下完成扫描,扫描速度要高出SLM约几个数量级。正是由于两者在输入能量和扫描速度两种工艺参数上的差异,从而导致SLM和EBSM产品具有不同的微观结构和力学性能。激光增材制造技术具有直接快速、可进行复杂结构成形的优点,尤其是针对难变形材料的复杂形状构件具有显著的优势,目前已经涵盖航空航天、生物医疗、汽车制造等多种领域[9-12]。由于铼和钒原料成本较高,近年来鲜有报道,因此本文概述了常见的钨、钼、钽、铌4种难熔金属在激光增材制造方面的最新研究进展,以期拓宽激光增材制造在难熔金属领域的应用。
1 钨及钨基重合金
钨是一种具有特殊固有特性(高熔点、高抗拉强度和低热膨胀系数)的材料,可用于在辐射环境下的高温、高热流密度组件,如准直器、未来核聚变反应堆的等离子体组件和高性能火箭喷嘴[13]。近些年来,学者们针对增材制造钨及钨基重合金的研究主要集中在控制孔隙率和裂纹的两大难题上,并获得了具有重要参考价值的研究成果。表1总结了近5年激光增材制造钨及钨合金的最新研究进展,其中包括所采用的制造技术、性能或组织特征以及应用领域等关键信息。可以看出在激光增材制造钨合金方面,主要采用的技术有选择性激光熔化(selectivelasermelting,SLM)、激光粉末床熔融(laserpowderbedfusion,LPBF)、激光熔化沉积(lasermeltingdeposition,LMD)、激光直接能量沉积(laserdirectedenergydeposition,LDED)以及激光烧结(lasersintering,LS)技术。在纯钨的激光增材制造研究中,针对样品内部存在孔隙的问题,钢铁研究总院谢琰军等[14]分析了SLM激光参数对钨块表面形貌和内部缺陷的影响,发现随着激光能量密度的增加,钨块表面更加平整,内部的孔隙将会减少。图1为不同激光功率下采用SLM技术制备钨块的表面形貌,可以看出低功率下的样品表面存在较多的未熔孔隙。
除了内部孔隙率的问题以外,裂纹也是增材制造钨的主要挑战。为了研究增材制造方向对于裂纹的抑制作用,清华大学李等[15]在LPBF过程中发现在样品中产生了极高的热应力,在平行增材样品和垂直增材样品中均产生了不同程度的缺陷,其中在垂直增材样品中出现了严重的熔化及飞溅现象,而在平行增材样品上仅观察到少量裂纹,这是因为在水平方向上所生长的柱状晶更加利于热量的传导。为了同时克服裂纹和多孔隙的问题,鲁汶大学Iveković研究小组[16]采用SLM工艺制备了高密度W和W-Ta零件,研究了在该工艺下钨及钨合金的熔化凝固行为。研究中发现,无论使用何种工艺参数和扫描策略,裂纹始终存在,然而随着钽元素的加入,裂纹形态变得不规则,晶粒尺寸也明显减小。在W的传统制造工艺中,采用IV族或V族过渡金属合金化可以抑制裂纹的发展并提高其固有塑性。例如,天津大学Wang[17]采用LPBF技术制备了W-6Ta合金,发现在预制体的晶界中含有丰富的纳米级气孔,并对抑制裂纹的机理进行了研究。结果表明,由于W-6Ta合金中存在多孔结构,纳米孔被困在晶粒内部,从而降低了裂纹的可能性。后来,在对纯钨和钨钽试样的开裂行为和显微组织研究中发现[18],W-Ta合金的裂纹数量和长度明显减小,晶粒得到细化,大量位错与Ta氧化物纳米颗粒缠结在一起。位错有利于塑性变形,而Ta清除氧杂质,有利于裂纹的减少,从图2可以看出,在添加6%Ta之后裂纹明显减少。空军工程大学Guo[19]采用SLM技术很好地解决了高密度钨基合金大规模复杂结构和薄板结构的成形问题,通过组织表征、XRD结果计算弹性常数,证实合金几乎没有出现宏观或微观裂纹。此外,钽的加入有助于提高钨合金的塑性和成形性,同时保持了较高的密度、硬度和强度,对高密度钨合金的应用具有重要价值。除了添加Ta元素以外,研究发现通过添加少量Re、Ti等元素也可以达到抑制裂纹的目的。日本富山大学Yamamoto[20]研究了LPBF法制备的钨铼(W-Re)合金的开裂行为和微观组织,发现随着铼含量的增加,柱状晶粒沿制造方向被拉长而逐渐细化。
近年来通过采用固溶强化和二次相纳米颗粒弥散强化使强化相与增材制造钨的固溶相结合,可以同时实现基体的强化和抑制裂纹[17,29]。清华大学陈金瀚[21]采用原位反应形成强化相的方式改善了LPBF制备钨块出现的裂纹问题,并且采用LPBF技术成功制备了钨-碳化钽(5%)的低合金钨块体。结果发现试样的孔洞减少、裂纹也显著降低,同时证明在添加碳化钽后材料的本征强度得到了显著提高。该小组随后分析了碳化物对增材制造钨的影响作用,研究中发现[22],加入TaC后合金的裂纹密度会明显降低,与纯W相比,W(Ta)固溶体和胞间碳化钨(W2C)在不同位置形成不同形态的胞状结构,为W组织的细化提供了有效途径。图3为纯钨和W-5%TaC的裂纹分布和内部微观结构,可以看出,与纯W相比,W-5%TaC的裂纹更加无序,密度也随之降低。
铁元素也被选为传统钨合金的添加剂,能有效地抑制钨基合金的孔隙形成,该合金通常会被用在聚变反应堆第一壁上,以延长其服役寿命[27-28]。北方工业大学Li[23]发现LMD法制备的W-20%Fe合金组织由W、Fe和Fe7W63个相组成。Fe7W6以壳状分布在钨相周围或以碎片形式分布在铁基体中,而正是由于Fe7W6相和钨枝晶的形成,显著提高了钨合金的硬度和脆性。激光工艺参数也是决定内部微观组织和缺陷的关键性因素,研究激光工艺参数对3D打印质量的影响是必不可少的。南京航空航天大学Sun[24]研究了激光工艺参数对W-20%Fe合金在LMD过程中热行为、熔化/凝固机制和组织演变的影响,在考虑了与温度相关的热物理性能基础上,建立了三维有限元模型。结果表明,随着激光功率的增加,熔池的截面结构变得更深,熔池底部和顶部分别形成柱状枝晶和等轴枝晶。
钨基重合金(WHAs)是一种由硬质钨相与基体相γ(W-Ni-Fe/Cu)组成的复合材料[30-31]。WHAs由于具有密度高、射线吸收能力强、硬度高等特性,应用于航空航天、武器装备、电子电气和核工业领域[32-33]。例如,如航空航天用陀螺仪转子、配重和减震材料、常规武器装备的穿甲弹弹芯以及热核聚变试验材料[34-35]。传统的粉末冶金技术具有低成本、原材料利用率高、生产效率高、节能环保的优势,能够直接生产形状独特的高性能产品,甚至能够实现材料的近净成型,但是目前粉末冶金制品仍然存在杂质含量高并且部分孔隙无法完全消除的问题,从而严重影响到产品的实际应用性能[36-37]。然而,利用直接3D打印技术制造钨基重合金(WHAs)仍不成熟,因此近年来众多学者围绕3D打印钨基重合金缺陷问题控制和致密化上进行了大量探索性工作。加州理工大学Wang[25]采用激光烧结(LS)技术研究了工艺参数对90W-7Ni-3Fe致密度的影响,发现激光功率和扫描速度是最关键的参数,随着激光能量的增加,孔隙由开孔变为闭孔,在烧结过程中,钨没有熔化,而是溶解在NiFe基体中,重排和溶解-再沉淀机制都是致密化的原因。为了解决W-Ni-Cu合金复杂形状的难加工问题,中南大学Wang[26]采用SLM工艺对W-10Ni-10Cu复合粉末进行了强化处理,发现在SLM处理后的样品中检测到非晶态W-Ni固溶相,这是由Marangoni迁移引起的,Ni-Cu相倾向于将液态W打碎成小颗粒,形成纳米晶。南昌大学Wei[27]采用激光直接能量沉积(LDED)技术制备了90W-7Ni-3Fe合金,发现样品的微观结构沿制造方向呈现明显的非均质性。LDED样品中基体相和W颗粒的硬度高于液相烧结样品,这一基本认识将为提高增材制造钨基重合金的力学性能和后处理优化提供依据。通过采用优化后热处理工艺可以提升激光增材制造样品的力学性能,中南大学Wei[28]采用优化后热处理工艺,制备了高性能激光烧结90W-7Ni-3Fe合金,W颗粒参与了基体-相协调变形,提高了界面结合强度和基体-相协调变形的延性。此外,发现短时间循环热处理可以使铸态试样的强度和塑性同时得到提高。图4为3种试样的代表性工程应力-应变曲线及室温拉伸性能(YS、UTS、EL),可以看出经过2种热处理(HT1和HT2)后的极限拉伸强度和延伸率都有所提升。
2 纯钼及钼硅硼合金
由于钼的难加工性和高昂的材料损耗,使其生产和发展受到一定的限制,而通过采用增材制造技术可以避免热机械加工并减少二次加工,具有缩短制造周期、提高生产效率的优势。近五年激光增材制造钼及钼合金的研究重点在纯钼及钼硅硼合金。奥地利因斯布鲁克大学Braun[38]研究了SLM技术熔炼钼、钨的工艺过程,发现SLM处理后的钼、钨中裂纹和残余气孔的成因是氧杂质的存在,氧以氧化钼/氧化钨的形式在晶界处偏析,从而导致热开裂。意大利国家核物理研究所Rebesan[39]通过调整LPBF的工艺参数制备了相对密度为99.5%的纯钼块,验证了完全致密试样的维氏显微硬度HV0.15(2077.6±176.4MPa)类似于商用钼。碳可以提高钼的塑性和晶界强度,科学上对这一现象的共识是,碳要么取代了晶界的氧杂质,要么抑制了氧向晶界的扩散。为了阐明碳化物与氧杂质及钼基体相互作用的机理,因斯布鲁克大学Kaserer研究小组在降低激光增材制造钼合金中的孔隙率和裂纹数量方面先后进行了大量研究工作,通过添加碳同时提高了钼的塑性和晶界强度。该小组首先采用新的钼粉合金化概念,用SLM法加工出具有粉末冶金材料力学性能的钼。发现添加质量分数0.45%的碳后的钼合金会导致组织过冷,从而使材料的凝固方式由平面状向胞状转变,这种组织上的转变可以使致密度、硬度和抗弯曲强度均得到提高[40]。随后该小组在LPBF增材制造工艺中,制备了碳质量分数0.45%的钼合金,确定出碳化物为正交晶ζ-Mo2C,ζ-Mo2C与α-Mo呈半相干界面。α-Mo/α-Mo界面和α-Mo/ζ-Mo2C界面均未发现裂纹。LPBF工艺生产的纯钼具有外延生长的粗大柱状晶结构,大角度晶界处有裂纹,经氧偏析脆化[41]。为了研究碳含量对激光增材制造钼合金的力学性能的影响,该小组研究了5种不同的钼碳合金的晶粒尺寸、抗拉强度和硬度[42]。研究结果表明,高碳含量下的晶粒细化归因于热过冷和结构过冷的增加。过冷允许颗粒在底层凝固层上成核生长,最快生长方向比外延生长的晶粒更接近热梯度,从图5可以明显看出,孔隙率和裂纹数量随含碳量的增加而减少[42]。
钼硅硼(Mo-Si-B)合金具有高温力学性能好、抗蠕变能力强和优异的抗氧化性能,因而被认为是发动机中镍基高温合金的替代品之一[43-44]。目前,制备Mo-Si-B合金主要有2种方法:电弧熔炼法和粉末冶金法[44]。电弧熔炼具有设备简单、能耗低、瞬时合成等优点。然而,在制备的材料中可能出现空洞和微裂纹。相比之下,粉末冶金法制备的Mo-Si-B合金的微裂纹少,组织相对均匀,它在室温甚至在1200℃下都表现出较高的强度,但它可能含有许多含氧量高的腔[45]。增材制造技术可以集成复杂的冷却结构,这不仅可以使涡轮叶片的材料更加优越,还可以使涡轮叶片的冷却系统更加高效。这种优化的材料和改进的冷却系统的结合将导致运行温度的显著提高,从而显著提高现代燃气轮机的效率[46]。激光增材制造的Mo-Si-B合金具有较为复杂的相组成结构,而这些结构将会对材料的性能起到决定作用,因此必须对激光增材制造后各相之间的相互作用进行深入研究。德国马普研究所Makineni[47]在激光增材制造的Mo-Si-B合金材料的凝固组织中发现主要相为枝晶α-Mo相,枝晶间的混合相为Mo5Si3(T1)+Mo5SiB2(T2),而非预期的平衡相Mo3Si+Mo5SiB2(T2),这种相组合可以提高其蠕变性能,同时证明了氧化物颗粒主要在枝晶间成功分散,导致了较高的压痕断裂韧性。马格德堡大学Schmelzer[48]首次论证了利用LMD工艺打印Mo-Si-B粉末材料的可行性,并对所制备的多相Moss-Mo3Si-Mo5SiB2的可打印性和显微组织演变进行了详细的分析。结果表明,LMD加工材料的硬度可与粉末冶金(PM)生产的Mo-Si-B合金相媲美。德国亚琛工业大学Fichtner[49]首次系统研究了采用LPBF制造高熔点近共晶Mo-Si-B合金的工艺,对近共晶Mo-Si-B合金进行气雾化处理,并对粉末进行分析,确定了制备无裂纹样品的合适工艺参数。在力学性能方面,确定了在潜在应用温度下的韧性-脆性转变温度和蠕变速率。西安交通大学Ma[50]通过正交试验研究了SLM参数对Mo-Si-B合金相对密度和样品缺陷的影响,发现层厚对相对密度的影响最大,其次是激光功率和舱口间距,扫描速度对相对密度的影响最小。通过调节SLM参数,可获得相对密度大于99%的致密Mo-Si-B样品。此外,SLM作用下的Mo-Si-B合金中存在大量的晶间裂纹,这些裂纹可以通过衬底预热来调节。从图6可以看出,随着基体预热温度的升高,试样的抗压强度也随之升高,重要的是基体在400℃预热时,水平截面上的裂纹几乎消失,裂纹的减少在一定程度上提高了试样的压缩性能。
3 铌硅及铌钛系合金
铌硅基合金由于其较高的熔化温度(>1750℃)、相对较低的密度(6.6~7.2g/cm3)、较高的高温强度和良好的抗蠕变性能,已被考虑取代镍基高温合金而作为新一代航空发动机的热截面材料[51]。然而,有限的塑性变形能力和较低的常温断裂韧性是目前限制其应用的瓶颈之一。随着激光增材制造的发展,激光增材制造Nb-Si、Nb-Ti系合金逐渐进入了人们的视野。激光功率是目前研究增材制造的Nb-Si系合金激光工艺参数的热点问题,圣彼得堡理工大学Goncharov[52]以机械合金化粉末为原料,采用LMD技术在不同激光功率下对金属样品进行激光加工,发现在500W激光功率下样品的微观结构由Nb、Nb3Si的固溶体和Ti的枝晶链组成;当激光功率增加到1400W时,Ti溶于Nb中,枝晶链消失,Nb5Si3硅化物稳定。北京航空材料研究院刘伟等[53]对LMD技术制备的Nb-16Si合金的微观组织和相组成进行了详细研究,发现激光功率对相组成不会造成明显影响,亚稳态的Nb3Si相和NbSS(niobiumsolidsolution)相的形成是由于在高能激光束的作用下硅粉和铌粉发生了原位反应。图7为不同激光功率下制备的Nb-16Si合金微观组织,可以看出随着激光功率的增加,Nb-16Si合金中的NbSS+Nb3Si共晶组织和先共晶NbSS相均得到了细化。
Nb-Ti系合金由于其生物相容性和低弹性模量,它可以用于医疗领域[54-55]。圣保罗大学Guzmán[56]采用LPBF工艺并结合等离子体雾化(PA)和氢化物脱氢(HDH)制备了4种不同扫描策略的Nb-47Ti合金样品,并对间隙元素含量进行了比较,发现在体心立方(bcc)结构的相基体中,熔体和胞状枝晶形成了相似的组织。圣保罗大学deMouraNobre[57]采用LPBF工艺通过控制激光功率和扫描速度参数来提高金属生物材料的杨氏模量。织构分析表明,激光功率和扫描速度越高,表面近立方织构越明显,杨氏模量越小。
4 医用多孔金属钽
钽具有良好的生物相容性,是一种重要的医用金属材料。激光增材制造技术由于具有快速、近净成形复杂零件的优点,已成为纯钽材料制造领域的研究热点。生物相容性是医用多孔钽亟待解决的核心问题,华盛顿州立大学Balla小组[58]采用激光近净成形技术,通过调整设计孔隙率制造出相对密度为45%~73%的多孔钽,并且证实多孔钽的细胞粘附与繁殖能力优于多孔钛。随后,该小组又对比了激光增材制造多孔Ta和Ti6Al4V(Ti64)的生物相容性,发现多孔Ta和表面修饰的多孔Ti64植入物在植入5周后通过无缝骨材料交锁实现早期骨整合的性能相当,而多孔Ta在术后12周的骨质形成方面具有持续和延长的疗效[59]。为了提高骨的结合性能,华盛顿州立大学Bandyopadhya[60]利用LENS技术成功地在钛表面沉积了一层钽涂层,与Ti表面相比,Ta涂层表面具有良好的细胞粘附和生长能力,细胞外基质形成丰富。但是,由于孔隙和涂层与基体之间缺乏锐利界面,这些致密的Ta涂层不会承受低的抗疲劳性能,这是用于增强早期生物固定的多孔涂层的主要问题。鲁汶大学Wauthle[61]首次采用SLM技术制造了多孔钽样品,经过测试发现多孔钽的力学性能非常接近于人体骨骼。与多孔Ti-6Al-4V结构相比,SLM制造的多孔钽具有优异的骨传导性能,且具有较高的归一化疲劳强度和较高的延展性。图8为采用SLM技术制造的医用多孔钽材料。纽约特种外科医院DeMartino等[62]为了验证多孔钽植入假体的稳定性,对植入人工髋关节的标准多孔钽进行了长达15年的临床跟踪,充分验证了多孔钽植入假体的稳定性。
国内在激光增材制造医用多孔钽材料方面也取得重要进展。中南大学Zhou等[63]发现采用SLM打印纯钽材料时发现激光扫描速率过快会使材料内部形成微孔隙,而过低的激光扫描速率又会引起层间的微裂纹。北方工业大学Guan[64]采用LMD工艺应用于2种不同间隙元素含量的钽粉的制备,研究了LMD试样的微观结构和力学性能。结果表明:钽样品具有接近完全致密的大柱状晶粒,生长方向与沉积方向略有偏离,LMD制造的钽硬度HV高达2940MPa,主要是由于间隙元素氮和氧具有固溶强化的作用。苏州大学的李洋等[65]采用SLM技术制备了多孔钽、多孔钛合金及多孔316L不锈钢等医用多孔金属材料,随后对各种多孔材料的生物性进行对比后发现多孔钽表面的细胞增殖能力强于其他的多孔医用材料。杨柳[66]等完成了世界首例增材制造个性化多孔钽金属垫块植入物全膝关节翻修手术。重庆润泽医疗有限公司采用SLM技术与高温烧结结合的方式,制造了满足植入体的多孔钽[67-68]。
5 总结与展望
激光增材制造技术由于具有高效快速、生产周期短、绿色加工的优势,是目前制备难熔金属的热点方向之一。但是,由于激光增材制造技术发展历史较短,尚存在制造成本高、工艺不稳定、缺乏系统化及标准化等问题,仍然制约着激光增材制造在难熔金属领域的应用。本文阐述了不同激光增材制造技术在难熔金属上的应用,尤其归纳了近5年来的最新研究成果,并得出以下结论:
1)激光增材制造技术为制造难熔金属复杂构件提供了新的发展思路,目前在制造钨及钨基重合金、纯钼及钼硅硼合金、铌硅及铌钛合金和多孔钽等方面取得了较大进步。
2)激光增材制造难熔金属的成熟度还有所欠缺,其中包括工艺和设备两方面,尤其是在裂纹抑制和降低孔隙率两大难题上仍需系统且深入的研究,解决该问题对于推进大规模工业应用有极大的促进作用。
3)降低原料成本和制造成本仍然是激光增材制造技术发展的主要方向,尤其是针对医用多孔钽材料,需要在控制原材料质量和短流程加工两方面进行深入的基础研究,达到降低成本的目的,从而造福更多的患者。
4)激光增材制造难熔金属还有巨大的开发潜力,随着增材制造设备的优化升级,将会大幅度提升产品的生产效率和精确程度,其中激光增材制造与其他技术相结合可以达到事半功倍的效果,这也可能是激光增材制造技术未来的重点发展方向。
参考文献:中图法分类号:TG 146.4+ 1
文献标识码:A
文章编号: 1002-185X(2023)05-1943-11
星尘科技专注于稀有难熔金属粉末的制备,采用射频等离子球化技术对金属粉末进行高效球化处理,显著提升粉末的流动性和松装密度。通过激光增材制造技术,球形粉末可实现高精度、高性能的复杂部件成型,尤其适用于航空航天、医疗植入等高端领域。
公司依托自主研发的射频等离子系统,能够处理钨、钽、钼等难熔金属,粉末球形度高、氧含量低,满足增材制造对材料的一致性和可靠性要求。星尘科技致力于为工业级3D打印提供高品质金属粉末解决方案,推动尖端制造技术的发展。